The Technology of the Production and Distribution of Oxygen and other Gases
The production of oxygen and related gases in industrial quantities was made possible by development of plants which could separate air into its constituent components. To achieve this the following had to be achieved:
- cool air had to cryogenic temperature to achieve liquefaction
- construct the cryogenic equipment from metal that would withstand very low temperatures at pressure.
- use materials and processes which would ensure safety when in contact with oxygen
- develop compressors for high pressure and product handling
- use insulation to contain the highly volatile liquefied gases
- remove carbon dioxide and water vapour from the feed air which would block the plants
The early plants which George Kinman described delivered 2400 m3 per day, were made from copper, removed carbon dioxide and water chemically and had all reciprocating machinery. Two plants were needed because in those early days as the plant became blocked with solid carbon dioxide it was simply stopped and left to warm up while the other was started and ran.
Air going in was cooled by the gases going out and the actual separation was achieved in a distillation column. An ingenious refinement was the use of a double column - the lower part being at high pressure and the upper part at low pressure enabling complete separation of oxygen and nitrogen.
Though the general principles remained the same, the large 'tonnage' plants producing over 500000 m3 per day which were used from the 1960s were made of aluminum/magnesium alloy with moisture and carbon dioxide removal in the passages of heat exchangers cooled by outgoing gases and the passages cleared of these deposits by outgoing 'waste' gas. (see flow diagram).
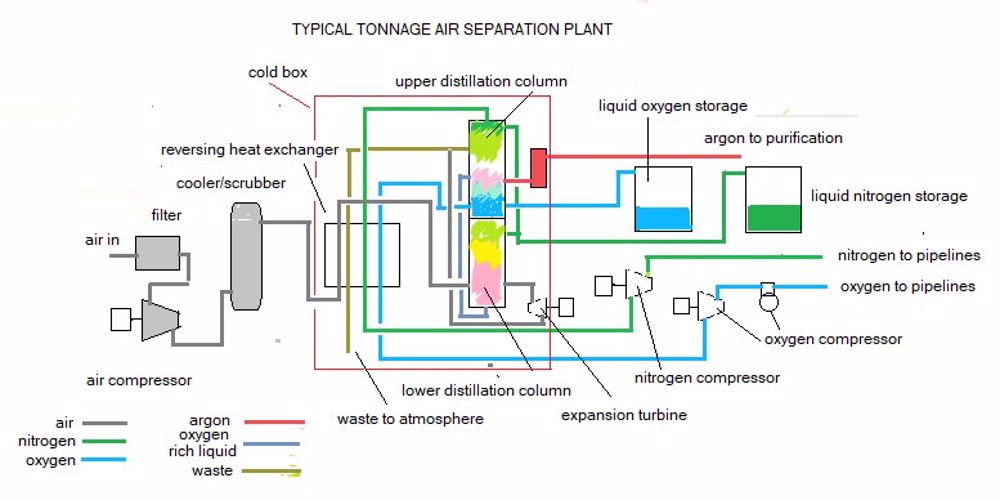
A side column taking a stream from a selected point on the upper column removes argon as a product. This argon is treated separately to achieve the desired purity. The designs vary among different plant manufacturers (e.g. using molecular sieves instead of reversing heat exchangers) but the overalll concepts are the same.
In the early plants the cooling (or 'cold production' as it is termed) was achieved by expanding high pressure streams in reciprocating engines, the expanded gas being cooler than the ingoing. Modern tonnage plants use turbo machinery throughout.
The entire cryogenic section of the production plant is housed in a large closed structure called a 'cold box' filled with expanded perlite insulation in place of the slag wool used in the early small plants.
Gaseous oxygen is compressed in reciprocating compressors to feed pipelines. Originally because of its reactivity the oxygen had to be compressed wet and then dried but the advent of suitable inert self-lubricating materials such as fluon for compressor components enabled dry compression.
The other main product, nitrogen, is compressed to feed pipelines. Because this is for safety use, 100% continuity of supply is critical.
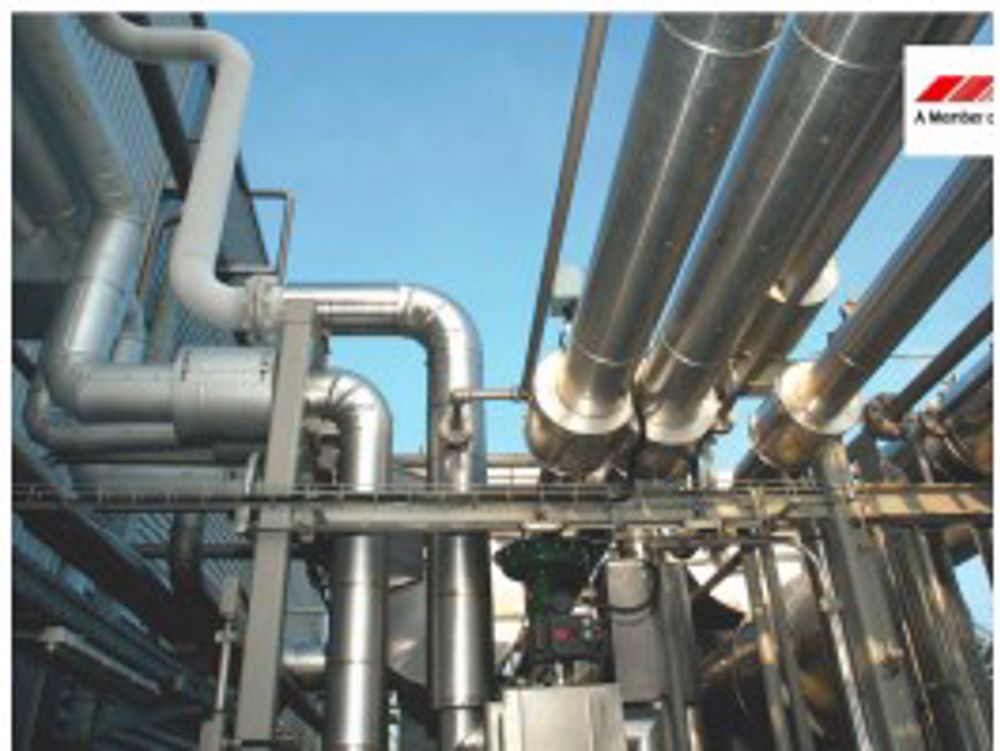
In the early days liquid storage was very simple with copper tanks insulated with slag wool but now tanks on production sites hold hundreds of tons and are insulated with perlite while tanks on customer premises are pressurized, stainless steel and vacuum insulated (like large vacuum flasks). Similarly road tankers (and rail) are large and vacuum insulated as are smaller transportable liquid vessels.
Pipelines are extensive with special cleaning and degreasing procedures for oxygen service and cathodic protection against corrosion with regular inspection.
By 1970 and beyond other techniques, usually small scale on site, for production of gases were emerging, computer control of plant arrived and environmental issues became ever more important.
Where stringent purity was not required and very large flows were not required, on-site PSA (pressure swing absorption) plants were becoming more common.
Electronics industry
The demands of the electronics industry are in a class of their own. In products such as printed circuits where a few misplaced atoms can cause failure a whole new ultra-clean technology has been developed. Gases which include, nitrogen, arsine, phosphine and silane are manufactured to extreme levels of purity and the polished lines which carry these to the process are subject to highly sophisticated cleaning procedures
Medical
The use of oxygen as a 'life saver' in medicine is well known but a relatively recent key development in medicine has been that of imaging, particularly MRI (magnetic resonance imaging) This relies on an intense magnetic field. The electric current in the coils which surround the patient is huge and is made feasible by cooling the coils to a level where they become superconducting thereby not generating vast amounts of heat. To do this they are immersed in liquid helium at 4°K (-269°C) and to hold the liquid helium at this temperature it too is immersed in a bath of liquid nitrogen. Helium with neon can be obtained from air separation but at present the majority is shipped from parts of the world where it occurs as a considerable proportion of natural gas.
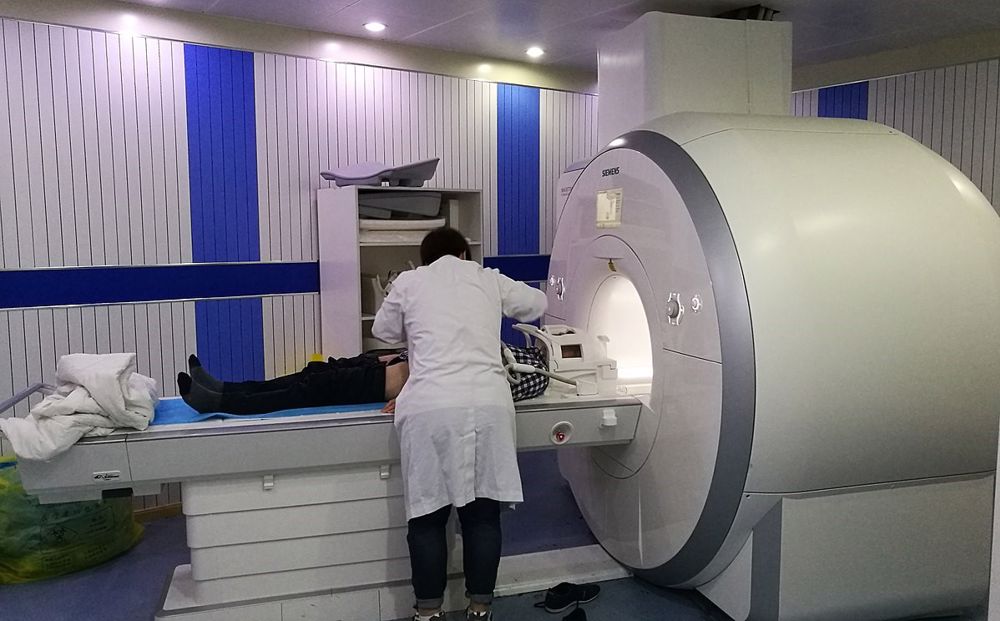
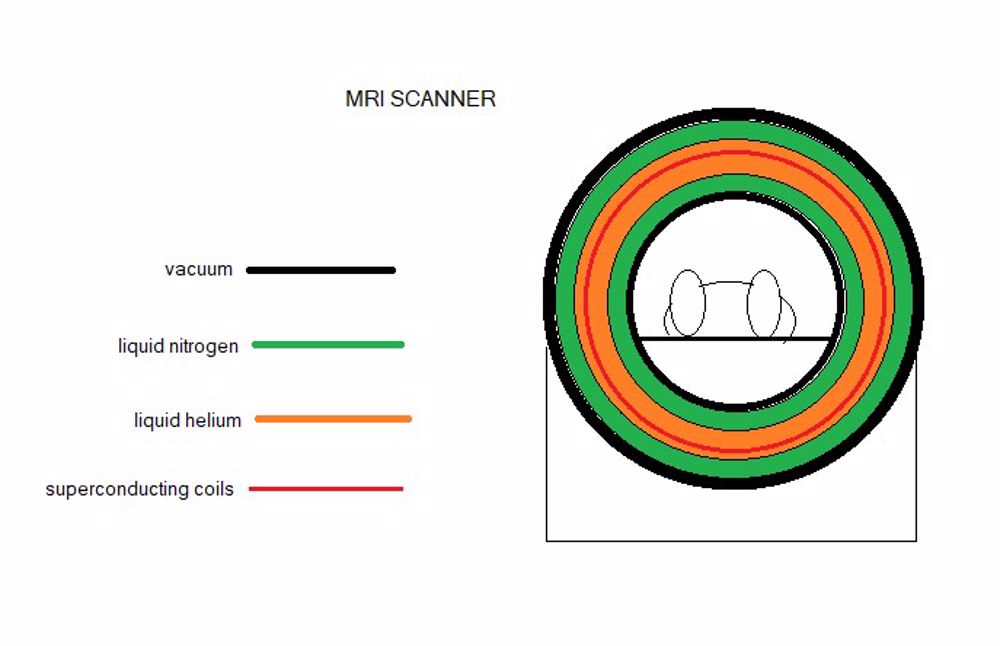
All the products and processes outlined above which have given so much to the health, wealth and well-being of society are the fruits of applying good sound chemical engineering practice.