The Story of Gasification
The gasification story covers virtually the full span of chemical engineering and still has a growing future. Gasification of fossil fuels produces hydrogen and carbon products which led both to the formation of the gas industry, and its use in refineries, power generation and hydrogen in ammonia production.
Over the subsequent 200 years the industry has seen many changes. Technologies have been developed with improvements in working conditions, safety, environmental performance, and efficiency to the point where modern processes are hardly recognizable as the descendants of the early retorts.
The initial use of synthetic gas from gasification was lighting – and later domestic heating. The London Gaslight and Coke Company was founded in 1812 and the use of town gas via gasification spread throughout Europe for well over 100 years. The start-up of the first commercial scale Haber-Bosch ammonia process in 1913 introduced coal-to-chemicals via the syngas route.
Gasification also found widespread use in oil refineries particularly in desulphurisation of transport fuels and hydrogen saturation of unstable cracked hydrocarbons and hydrogen formed the basis of chemical manufacture for example, plastics, ammonia (Haber) and methanol. The second world war saw gasification and the Fischer Tropsche catalytic process used at large scale for the manufacture of liquid transport fuels.
More recently, gasification has also found limited application in power generation (Integrated gasification combined cycle or IGCC). The high temperature and pressure of the reaction, which allows gases to be further processed for pure hydrogen production and the decarbonisation of the energy content of fuels through CO2 capture and storage. Recently, there has been much discussion about the need for hydrogen production, in which gasification and reforming could play its part.
The advance of gasification has depended on the development of large, normally vertical reactors by Industry, to bring the fossil fuel, i.e., coal, coke, refinery heavy products and waste into close contact with the oxidants. Chemical engineers have developed high-pressure synthesis technology as exemplified by ammonia provided an incentive to look for methods to improve the efficiency of syngas production from coal. A variety of proprietary designs for entrained flow, fluidised bed gasification, and the use of oxygen/steam has been developed. The holders of these designs drive the commercial market.
They are supported by academic research into the new applications of gasification, particularly for the processing of municipal and commercial waste streams. The recent interest in underground coal gasification and plasma gasification, and autothermal reforming of methane to large scale hydrogen production (blue hydrogen), when coupled with carbon capture and storage (CCS), are further developments that could extend the future for fossil fuels.
The commercial environment has changed, but today, gasification produces some 25% of the world’s supply of synthetic ammonia and about one third of the world’s methanol. There are over 600 gasifiers in operation in about 230 projects with a further 750 or so planned or under construction in about 160 individual projects. The thermal rating of currently operating gasifiers is just over 100 GW with about 140GW in planning or under construction. Research and development continues on five continents.
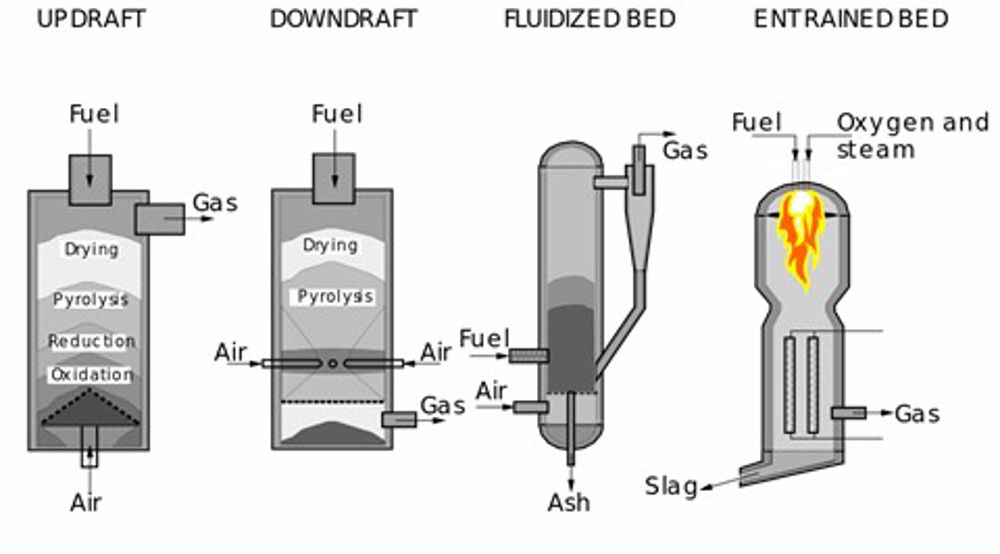