Three Accidents and Many Lessons – Continuing to learn and improve Process Safety
Chemical Engineering, which underpins the manufacturing for chemicals, fuels, pharmaceuticals, personal care and so much more of the products and materials that we use every day, usually only hits the headlines when there is a major accident. Such disasters are always a tragedy and it is the responsibility of chemical engineers to design and run manufacturing facilities as safely as possible. Learning from why accidents have occurred is all part of improving future processes and making them safer. And we are getting much better at this; for instance, in 1981 the UK manufacturing fatality rate was 2.0 per 100,000 workers; by 2018/19 this was down to 0.9 and in 2019/20 it was 0.5. By contrast for agriculture/forestry/fishing the corresponding figures are 9.5, 9.2 and 6.0 and for the workplace as a whole 2.1, 0.5 and 0.3. Whilst it is good to aspire to the outstanding safety record of the airline industry (in 2019 there were 0.013 fatalities per 100,000 passengers), this shows that substantial learnings and improvements have been made over the decades in the safety of chemical manufacturing processes.
I can illustrate this journey through three major incidents with which I have been connected, where the lessons learned have changed the face of Process Safety over the past few decades. Over my career from the early 1970s, Process Safety practice and performance has generally improved – but with progress punctuated by tragic major accidents which emphasise that there is never room for complacency and, however small, the chinks in the armour of risk management can be readily breached without careful and watchful diligence. These must be used by chemical engineers to understand why the hazards and risks which are inevitable ingredients of any industrial process are sometimes not fully identified or robust barriers not put in place to prevent them wreaking havoc.
The story starts with my first year as a young lecturer at Imperial, 1974, and the Flixborough caprolactam plant disaster on 1st June, which sent shock waves through the industry about the large potential for similar accidents on plants where poorly controlled modifications had been carried out. This incident coincided almost exactly with the passing of the Health and Safety at Work Act in July 1974 and the subsequent arrival of the Health and Safety Executive (HSE) in 1975. I recall the involvement of my Imperial chemical engineering colleagues, particularly Douglas Napier, in the aftermath of Flixborough and the training of vast numbers of new inspectors for HSE. The recommendations from the Advisory Committee on Major Hazards, which examined the broader implications of Flixborough for all major hazard installations, had a large impact on the processes of the HSE and the shape of the regulatory framework going forward. Most notable was the game-changing adoption of the goal-oriented safety case approach to replace more prescriptive, box-ticking earlier approaches and the requirement for the process operating company to take full responsibility for identifying and mitigating all the process risks on their plant.
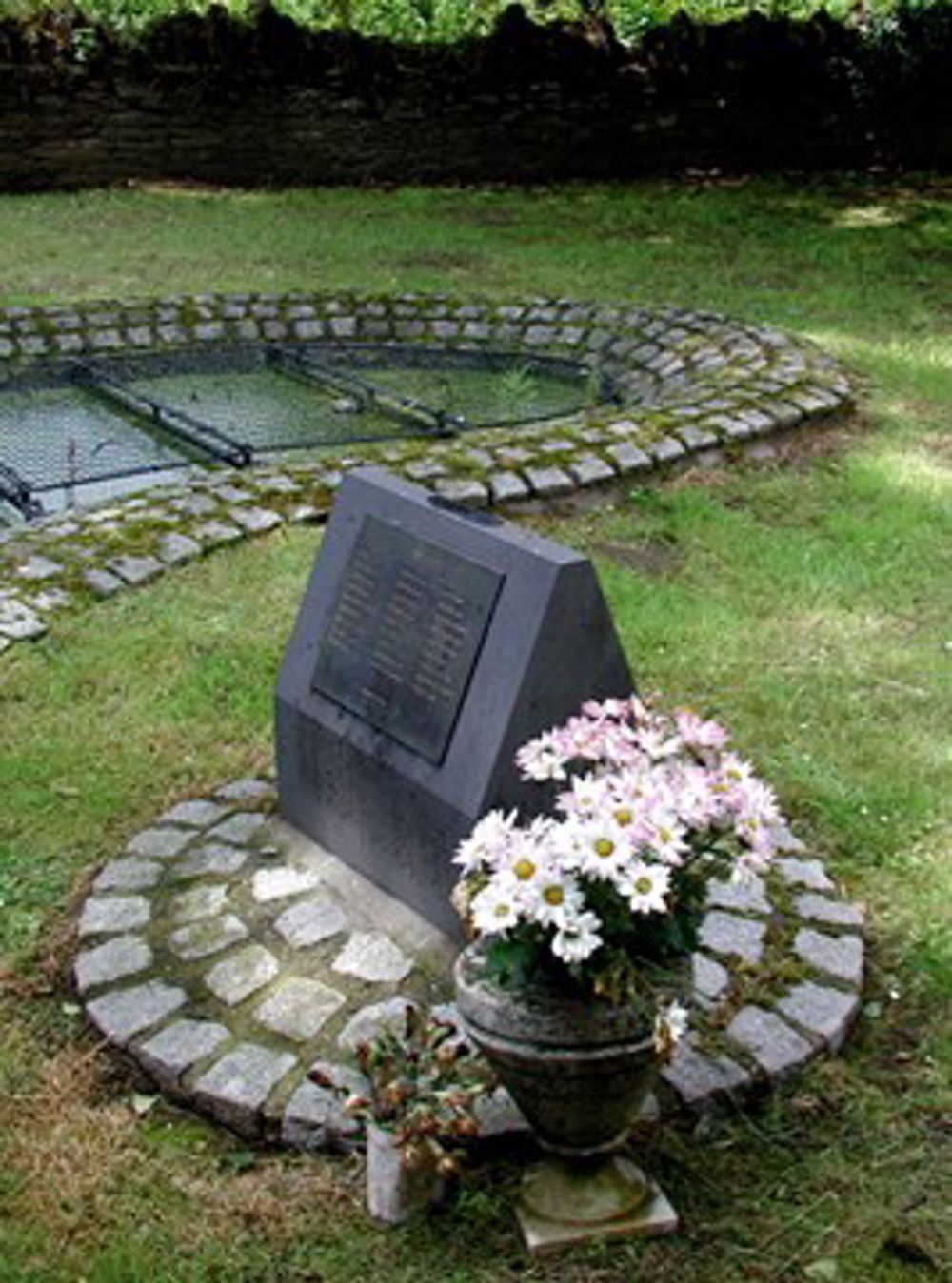
The next incident comes after I had left Imperial to work for Schlumberger in the oil and gas industry. Just three years into that job in 1988, the disaster on the Piper Alpha oil platform occurred. The multiple explosions driven by gas and condensate leaks, arising from poor communication of work permits leading to the use of a leaking pump which had been set aside for maintenance, led to the tragic death of 197 people, the world’s largest offshore oil and gas disaster. I recount how my former Imperial colleagues Stephen Richardson and Graham Saville were key technical witnesses at the resulting Cullen Inquiry and how their thermodynamic-fluid mechanical modelling of abrupt gas and condensate depressurisation has since been enshrined in the Blowdown software which has been used for design and operation of condensate flow systems on over 100 installations worldwide. Amongst Cullen’s 106 recommendations was that HSE should be the single regulatory body to enforce safety offshore as well as onshore, extending the use of the safety-case approach to those operations as well.
After returning to academia at Imperial in 2005 after 20 years in oil and gas, I became involved in explaining to the public through television, radio and press interviews why the 2010 Deepwater Horizon disaster in the Gulf of Mexico happened and how BP and their partners were trying, unsuccessfully for a long time, to cap the well. I gave over 50 media interviews in the 87 days it took to stop the oil flowing into the Gulf, resulting in the largest oil spill of all time, with huge ecological and economic consequences. Then to my surprise in 2011 I was asked to chair the review of the UK Offshore Regulatory System to recommend changes to ensure that everything possible is done to ensure that such a disaster never occurs on the UK Continental Shelf. Amongst the recommendations was that safety (enforced by HSE) and environmental (enforced by DECC) regulation should be brought together into a unified body, which eventually occurred with the creation of the Oil and Gas Authority and the Offshore Safety Directive Regulator in 2015. So another unwelcome major accident led to further integration of safety and environmental regulation and strengthening of the ability of the regulators to hold the hazards creators to account.
So through lessons learned from these three accidents (and from other accidents and near-misses of course) the process safety regulatory regime in the Uk and in many parts of the world has been refined to make risk identification and mitigation implementation increasingly robust, with accidents rarer and of lower impact. Process safety is at the heart of chemical engineering’s DNA; we have come a long way with continuous learning and improvement – but every incident shows there is no room for complacency! We must continue to develop better learning processes into the future, with more cross-referenced data and AI bound to raise the process safety bar still further.