Management of Vapour Explosion Risk in Polystyrene Manufacture
American plastics manufacturer Monsanto initially developed the Type A bulk process for the production of polystyrene using a 3-stage batch process, comprising 30% polymerisation in a jacketed agitated kettle providing cooling to remove the heat of polymerisation, followed by transfer of a now viscous mixture of polymerising styrene monomer into a filter press. The press comprised alternating open segments to accommodate the mixture separated by aluminium platens to provide heating or cooling. Finally, the cooled 150kg blocks of polystyrene were crushed in a hammer mill and bagged for sale as a moulding product for use to manufacture house hold and medical items. The plant was located in a fully clad building as was common practice for plastic manufacturing facilities of that time. During each batch there was a period when the reaction 'peaked’ out of control in the filter press, generating an explosive mixture of styrene vapour in air. While this process was operated by Monsanto for nearly 30 years the risks associated with routine explosive mixtures were not recognised until a number of fatal industrial accidents occurred in the 1960s and 70s.
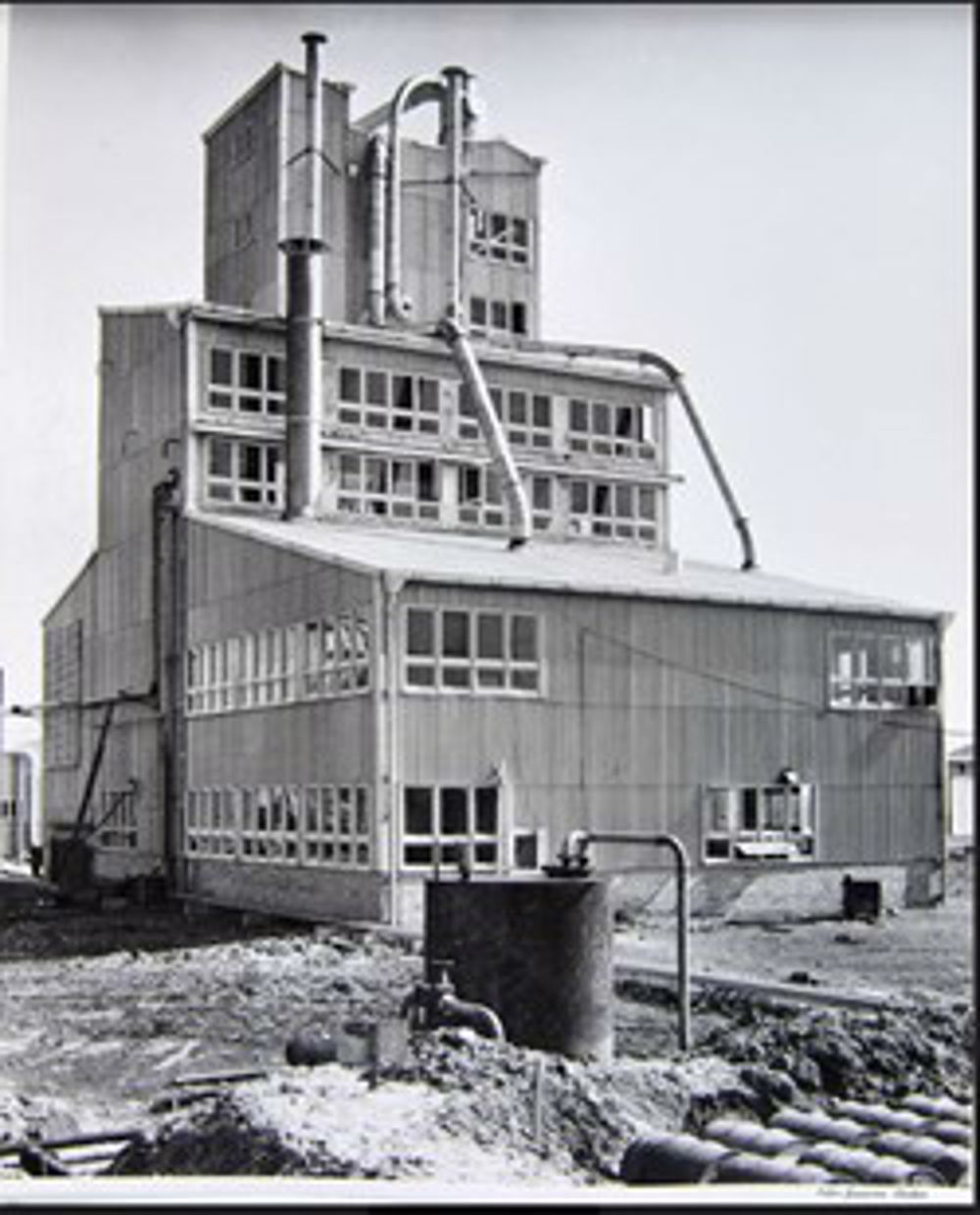
In 1953 a Type A batch crystal polystyrene plant was commissioned at Monsanto’s West Footscray plant using imported styrene monomer and Monsanto polymerisation technology. While the plant ran successfully for twenty years there were incidents, which may have resulted in a serous explosion due to limited ventilation within the building. The plant supervisor on one occasion saved the plant from an explosion when he entered the kettle floor in a full respirator suit to apply cooling water to the jacket following a failure to transfer a batch in time. The kettle's overpressure protection device a rupture disc, had ruptured releasing styrene fumes into the kettle floor room, but fortunately the explosive mixture failed to find a source of ignition.
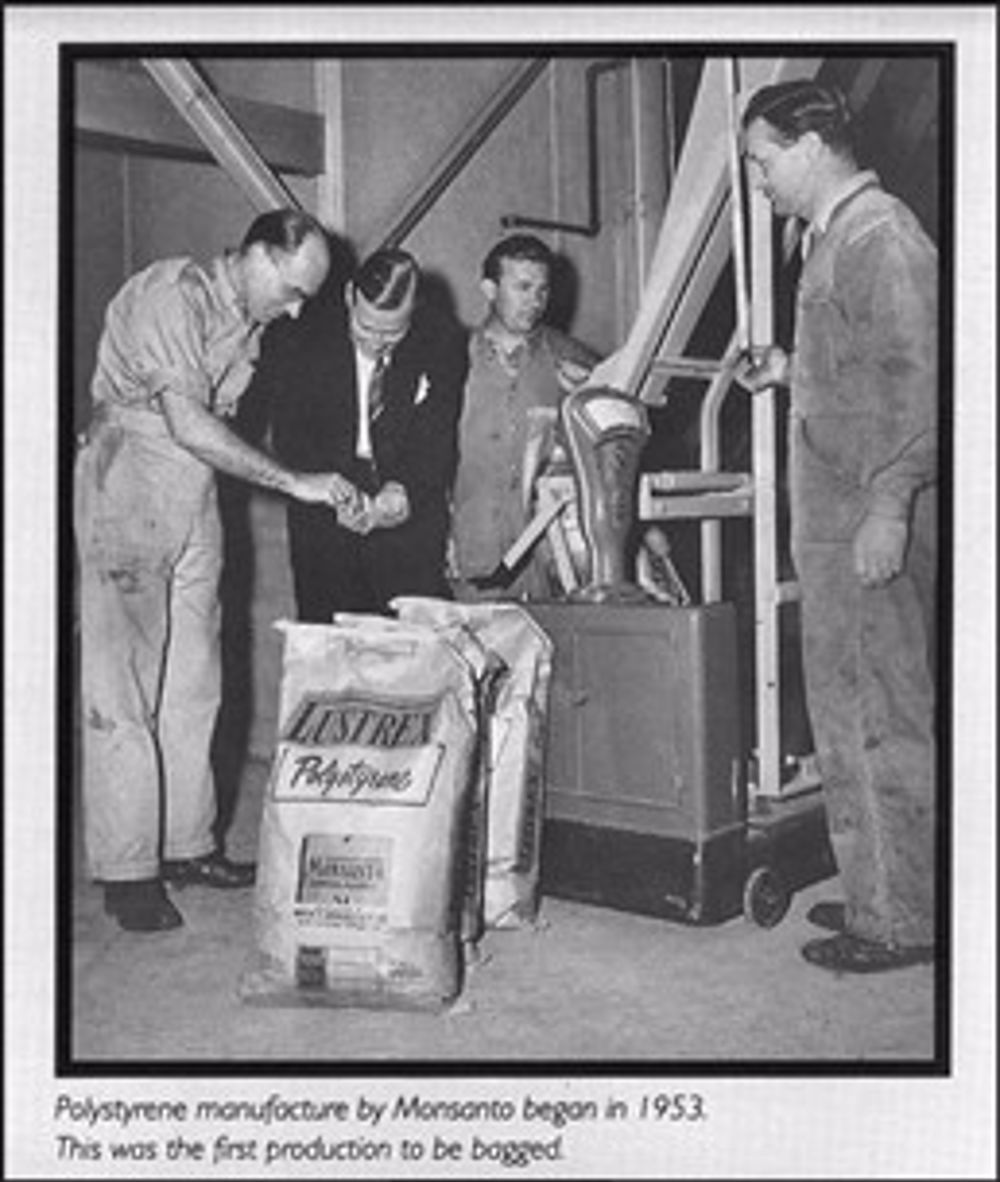
In 1966 at the Monsanto Type A polystyrene plant in LaSalle Quebec, a large styrene vapour cloud explosion killed 11 plant operators when a kettle temperature controller failure led to a runaway polymerisation reaction bursting a rupture disc on the batch kettle and relieving styrene vapour out a sight glass below the disc within the process building. This caused a vapour cloud above the explosive limit to form and subsequently ignite. Following this tragedy, a number of modifications were implemented worldwide by Monsanto including provision of an independent kettle high temperature trip, elimination of kettle sight glasses and separation of control rooms from the press and kettle floors. Additionally, Monsanto began work on a continuous polystyrene process, which minimised the likelihood of an explosive mixture accumulating in the plant, located in an essentially open structure. Five years later another styrene vapour cloud explosion at the press level in the Monsanto Zarate Type A plant in Argentina killed 2 operators when the press floor extraction fan failed leading to a vapour cloud explosion ignited by the fan’s chain drive and causing the collapse of the press floor onto the men working below. Type A plants around the world were shutdown, while incident investigations were completed.
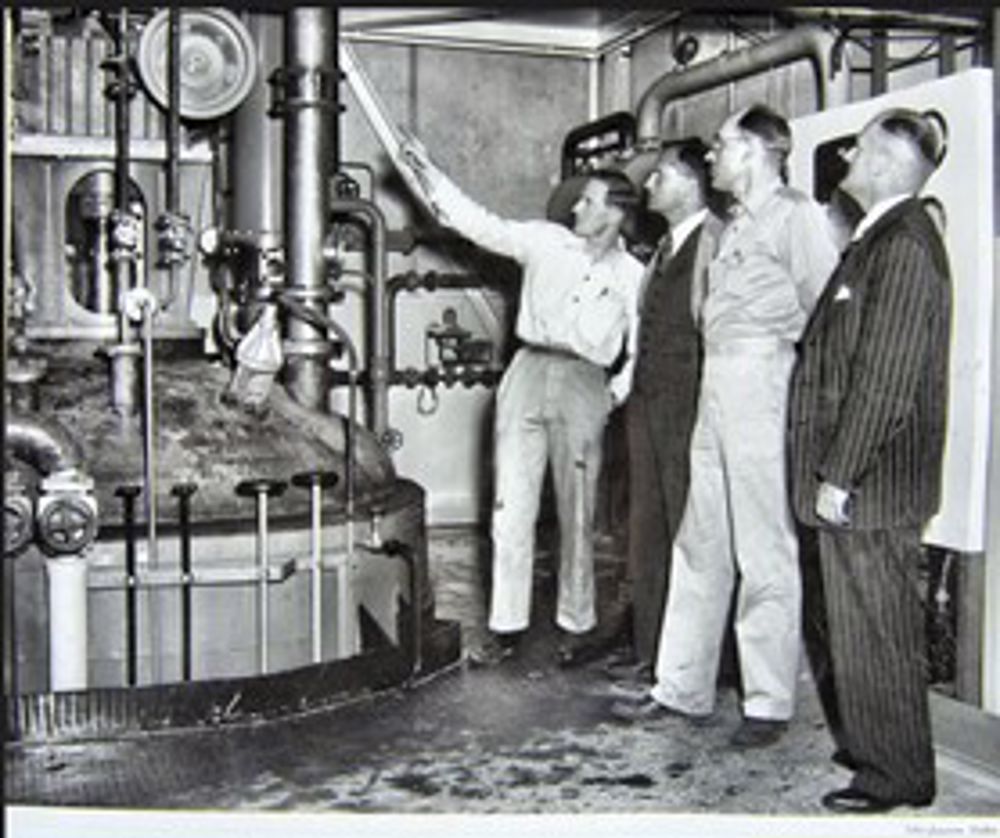
As a graduate chemical engineer in 1974 at West Footscray one of my first assignments was to undertake the Type A Safety Audit following the Zarate explosion against the required company safety standards, which initially didn’t seem a very exciting task. As it turned out this assignment gave me the opportunity to present my proposals for implementation of a project to address the shortcomings of the West Footscray Type A plant to the Plant Manager after only 8 months of engineering experience.
Prior to that time the hazards associated with loss of containment of flammable vapours were not fully recognized and as a result of the audit a 300k (AUD) project was proposed. The major aspects of the project involved opening up the building walls to reduce overpressure in case of an explosion and relocation of the old electrical switch room from below the press level. The plant supervisor of the 1950s by now CEO again saved the plant by approving the project in spite of the fact that the plant was scheduled for shutdown 18 months later. This followed start-up of a continuous polystyrene unit which with its reduced and contained inventory, controlled reaction rates and outdoor location minimised the risk of explosion and subsequent plant failure from flammable vapour cloud explosion.
Resources:
The Chemical Industry and the Australian Contributions to Chemical Technology published by the Australian Academy of Technological Sciences and Engineering in 1988 by Jan Kolm
A Batch Polystyrene Reactor Runaway: A Case History by Ronald J. Willey, PhD. PE. North Eastern University for the SACheM by CCPS-AICHE New York, New York, 2000
Photos of Depts 167 (Type A ), 75 (Type CI) and 81 (Type CC and CN)
Personal experiences 1974-1977