Systematic Hazard Identification Tool – Hazard & Operability Study (HAZOP)
One of the greatest aids provided for chemical engineers was the ability to systematically identify all hazards associated with a chemical plant. There are many hazard identification methods available, however, the one most used is the Hazard and Operability Study or HAZOP.
An important benefit of HAZOP studies is that the resulting knowledge obtained by identifying risks and operability problems in a structured and systematic manner, is of great assistance in determining appropriate remedial measures.
History
In the 1960s, the ICI pioneers of the technique (Trevor Kletz and others) considered how to tackle the issue of increasing complexity of plants, control systems and processes, and developed the guideword-based approach. ICI generated the method to do detailed process safety reviews of complicated process plants to test design integrity. People outside ICI soon realised that it was a good idea and since the 70s, it has been the process safety design testing system of choice.
In his book HAZOP and HAZAN, Trevor Kletz describes HAZOP as a “technique which provides opportunities for people to let their imagination go free and think of all possible ways a hazard might occur, but – to reduce the chance that something is missed – it is done in a systematic way, each pipeline and each sort of hazard is considered in turn.”
Method
HAZOP study is carried out when the process design of a plant is complete and detailed Piping & Instrument Drawings (P&IDs) are available. A multi-disciplinary team is used under the guidance of a trained and experienced study leader, who must ensure comprehensive coverage of the system under study. To facilitate this examination, the plant is divided into parts (called nodes) in such a way that the design intent or function for each part can be defined. The study leader is usually assisted by a recorder (called Scribe) who records all proceedings of the study.
For each part in turn, the HAZOP study team examines each property for deviation from design intent which can lead to undesirable (or desirable) consequences. This is achieved by a questioning process using predetermined guidewords. The role of the guideword is to stimulate imaginative thinking, to focus the study and elicit ideas and discussion, thereby maximizing the chances of study completeness. Examples of guidewords are as follows:
- Flow: No Flow, More Flow, Less Flow, Reverse Flow
- Temperature: More Temperature, Less Temperature
- Pressure: No Pressure, More Pressure, Less Pressure
- Composition: Additional Component, Component Missing or Change in Ratio, Complete Substitution
- Loss of: Power, Instrument Air, Steam, Nitrogen, Heating or Cooling
- Other Events: Static Electricity, Sampling, Steam Out, Nitrogen or other Purging, Chemical/Acid Treating
Once an undesirable consequence is identified, an action item is created to resolve the hazard. At the end of the HAZOP study, a report is generated listing all action items with names of persons responsible for their resolutions.
It is customary practice to reconvene the HAZOP team when all action items have been completed. This is to ensure that the resolutions of the action items are adequate. In the early days, the remedial actions were qualitatively checked by the team for acceptance. However, these days when the concept of acceptable risk is widely used, the team ensures that the resolution of the action items meet the acceptable risk criteria of the organisation (usually driven by the legislative framework of the country). A Layers Of Protection Analysis (LOPA) is commonly used to ensure acceptable risk level has been achieved.
Current good practice is to include HAZOP in a more comprehensive study called the Process Hazard Analysis (PHA), especially for existing plants. Although HAZOP takes up most of the analysis, other parts of PHA include:
- Incident Review – to ensure lessons from incidents on similar plants have been included.
- Plant Tour – to ensure good access, identify vibrating objects, ensure good fireproofing of structures, etc.
- Human Factors Screening Review – high level review to identify tasks which would require more detailed analysis by a Human Factors expert
- Facilities Siting Screening Review – to ensure no additional hazards exist for occupied buildings or no unauthorised temporary buildings are being used, etc.
- Management of Change (MOC) Review – to ensure the cumulative effect of all past changes do not create additional hazards.
- Mechanical Integrity (MI) Issues Review – to cover mechanical issues not covered by HAZOP e.g., suitability of pump seals, corrosion under insulation, etc.
Example
To demonstrate the HAZOP process, let us take the example of an overhead separation drum of a distillation column (diagram attached). A two-phase overhead mixture from the distillation column, after cooling, enters the drum. Gas liquid separation takes place inside the drum. The gas stream leaves the drum as the top product under pressure control. The liquid stream leaves the drum as the bottom product under level control.
Let us take the bottom product line for HAZOP study. This line contains block valves, a centrifugal pump, a non-return valve, a flow meter, and a level control valve. Now apply the guideword “No Flow” and identify reasons for no flow in the line. These will include:
- Block valve/s closed
- Pump not running
- Level control valve closed (by malfunction)
- No liquid level in the drum
The next stage is to determine the consequence of each of the above scenarios and ascertain if any of the consequences would be hazardous. Taking the case of the “Level control valve closed”- the pump will find a blocked outlet and will generate the maximum pressure (known as the shut-in pressure) possible by the pump. If the discharge line and the equipment including the control valve is designed to withstand the shut-in pressure of the pump, this situation is unlikely to lead to a hazard. The system should be able to withstand this short- term excursion especially if there is a low flow alarm warning the operator to act. If, however, the discharge line and the equipment cannot withstand the shut-in pressure of the pump, a pressure protection device or automatic pump shutdown on low flow may be required. In such a case, an action item will be generated and followed through as described earlier. The consequences of all other causes of no flow will be examined similarly. When all cases of no flow have been exhausted, the team will move to the next guideword e.g. “More Flow” and so on.
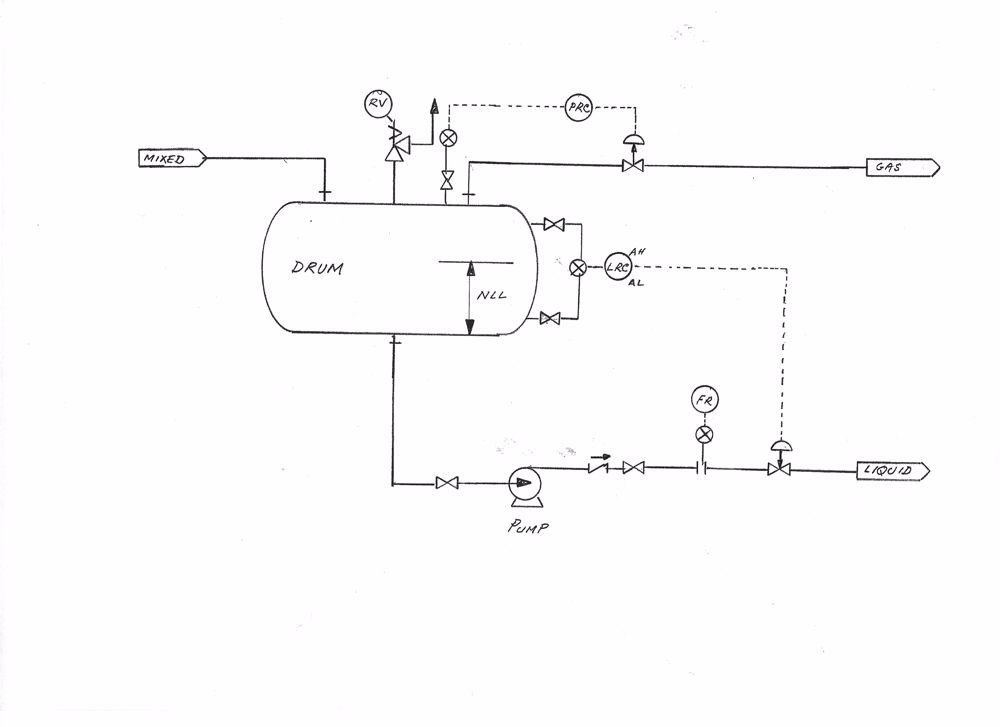
Future
HAZOP is here stay as the process safety design testing system of choice. However, the guideword driven principle has the potential to be used for any system which has a workflow. With further collaborative work and development, HAZOP could potentially be used to identify system weaknesses in other branches of engineering e.g., in an electrical distribution system. Also, other non-engineering processes, like banking and financial services, may also benefit by using HAZOP like examination.
Conclusion
HAZOP has become an essential part of good practice for ensuring integrity of process design. The study must be carried out with critical thinking in a frank and open atmosphere. The team carrying out HAZOP needs to be well trained and technically qualified. All these mean that HAZOP can be a time-consuming process. However, the benefits of the HAZOP process have been clearly demonstrated over many years. It is one of the most beneficial additions to chemical engineering (specially to process safety) in the last 100 years.
References:
IEC 61882 – Hazard and Operability Studies (HAZOP Studies) – Application Guide
Crowley, Connor – HAZOP in a World of Covid, The Chemical Engineer, August 2020
Kletz, Trevor – HAZOP and HAZAN