The wonder of Coal and its Products - continued
The Technology of Carbonisation and the Recovery & Refining of Biproducts
Coal occurs in a range of types from hard anthracite with high carbon and low volatile content through to lignite. Within this range lie coals suitable for gas production with lower carbon and high volatiles and coals ideal for making hard coke for the iron and steel industry while at the same time yielding valuable biproducts.
Early days
In towns-gas production coal was in the early days put into horizontal retorts and later in vertical retorts to produce towns gas, 'soft' coke and biproducts including coal tar.
Coke for the production of iron had to be strong and resist being crushed when placed in a cupola or blast furnace. This coke was made in beehive coke ovens, sealed chambers where where coal fed from above was heated by the volatiles burning above it. The retention of heat in the surrounding brickwork initiated the combustion of the new charge. When carbonisation was complete the doorway was broken open and the coke removed by hand. The doorway was then bricked up again ready for the next charge which was fed from wagons running on track above the ovens.
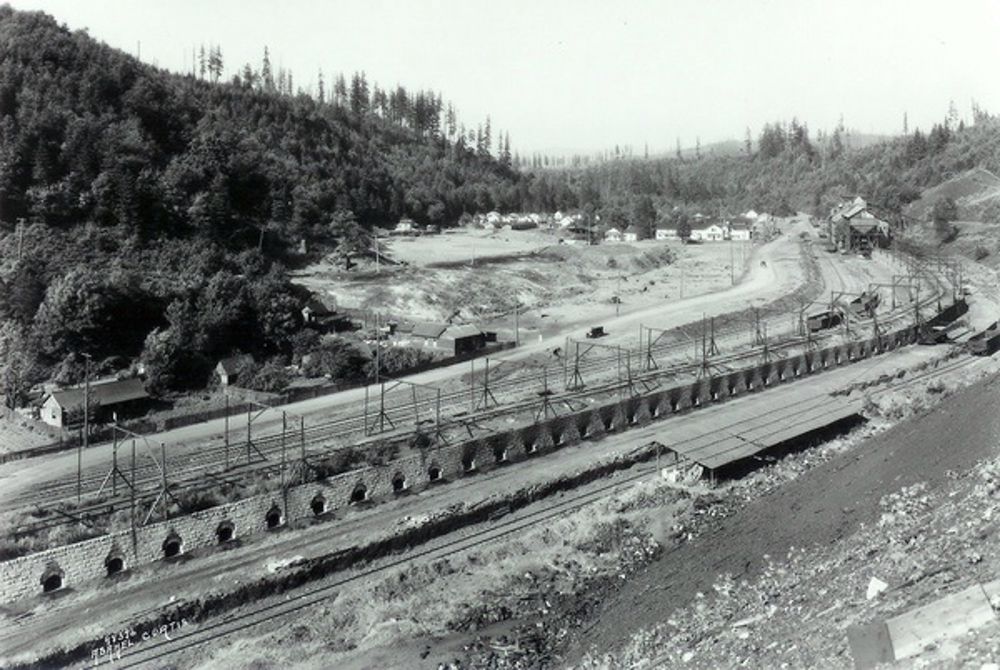
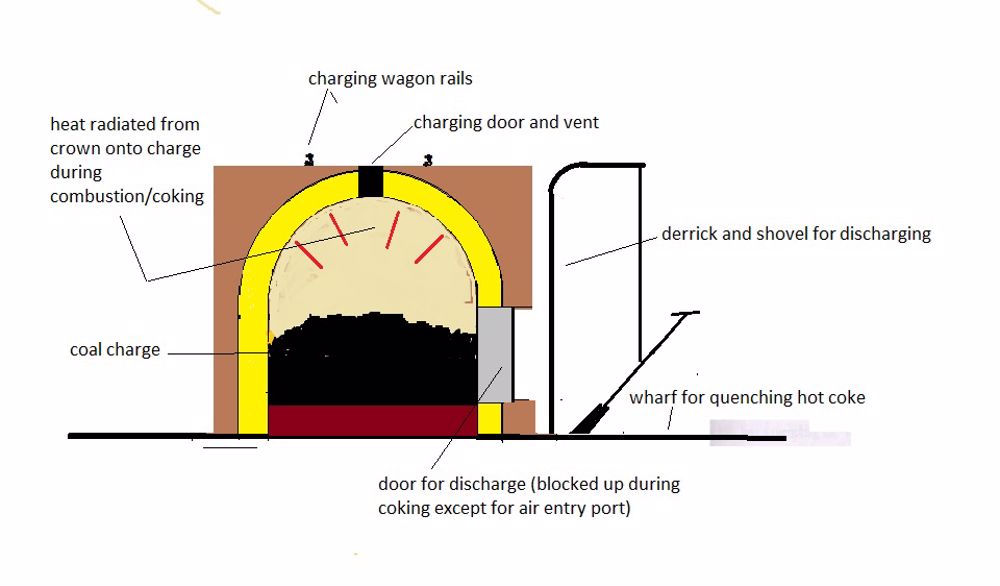
The coke produced in the beehive oven was large, hard and strong, ideal for use in foundry cupolas and blast furnaces.
However the process was labour intensive and wasteful. The next step was waste heat ovens where the gases were used to heat the oven and the waste heat was recovered for some other use such as steam raising.
The best example in the UK was Ottovale near Blaydon where there was a limited recovery of the valuable biproducts which can be derived from coal particularly tar. (I recall visiting this plant in 1955 and the cellar where the heating system fed the ovens was the hottest environment I have ever experienced in any part of the world or in any plant)
These plants were superseded by the modern version of coke oven plant. They were vertical brick chambers with heating flues between each oven using a proportion of the gas from the oven or in steel works complexes low calorific value blast furnace gas.
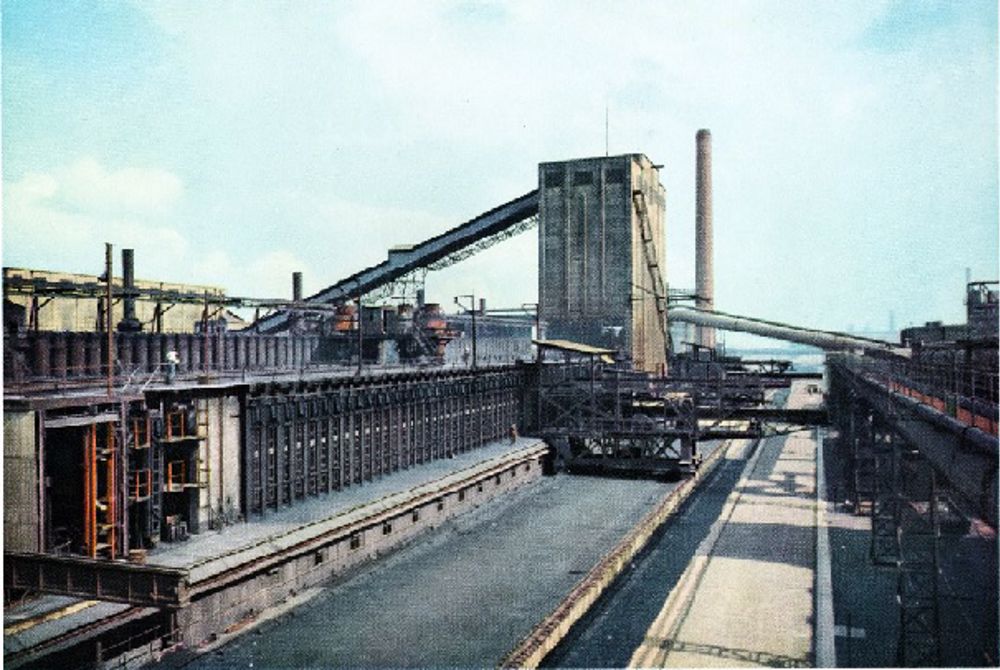
Modern coke ovens
By siting coke oven plant next to the steelworks which would consume the coke, an integrated system was possible. Coke (after grading) could be readily fed direct to the blast furnaces; low calorific value 'waste' blast furnace gas could be used to heat the coke ovens; coal gas could be fed to the steelworks for applications where a higher calorific gas was required. In the days of open hearth furnaces the coal tar was used as a liquid fuel atomised in the furnace burners. Excess coal gas from the system was purified and fed into the towns gas system.
The coking and biproducts processes covered most of the operations associated with chemical engineering - solids handling, crushing, heat transfer and recovery, gas handling, gas cooling, scrubbing, chemical reaction (ammonia removal and gas purification), distillation, gas compression and distribution, waste disposal.
Because of high flammability and explosion risk most of the process had to be carried out under carefully controlled conditions.
The coke ovens were ceramic brick chambers typically arranged in batteries of about 50/60 and the order in which the ovens were filled and emptied was carefully controlled. Each oven was about 13 metres long by 4 metres high by 0.4 metres wide with removable self sealing doors at each end . High fuel efficiency was achieved by heat recovery from the exit flue gases to the incoming air and lean fuel gas. The combustion air and the low grade gas were fed separately through regenerators. These were heated by the outgoing combustion gases (see diagram) and the fuel gas was fed through a pipework system below the ovens. The regeneration cycle was automatically reversed.
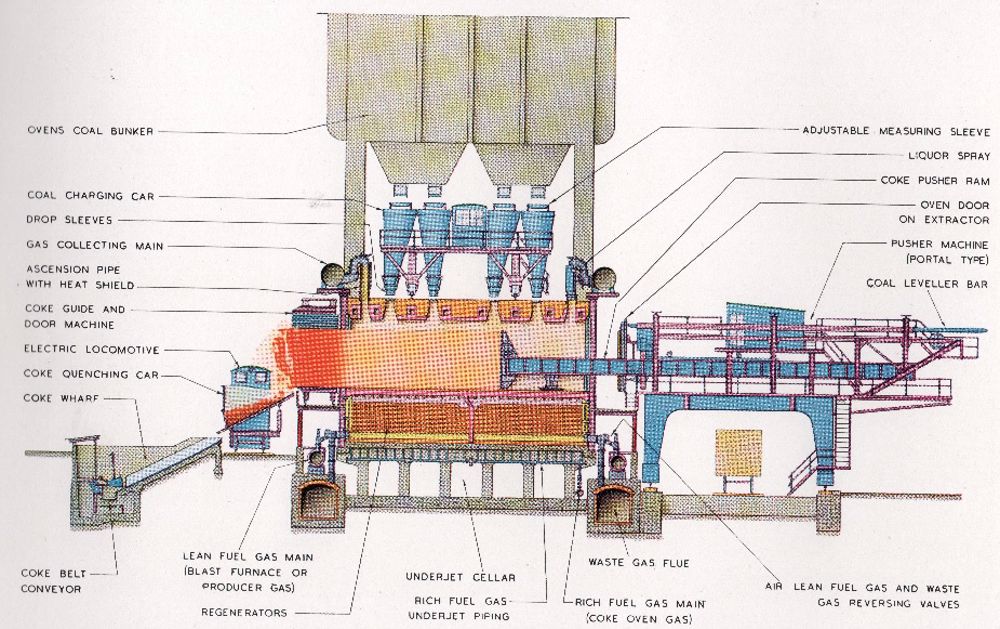
Coal was crushed and fed to a large overhead bunker holding up to 4000 tons. From the bunker each oven, with the removable doors at each end closed, was filled via a charging car through openings on the top of the oven. Before heating the charge was levelled by a beam fitted to the pusher machine.
At the end of the heating cycle when the coking process was complete, the mechanically handled doors were opened. The red hot coke in the oven was then discharged by the 130 ton pushing machine which forced the coke out of the oven through the coke guide into the coke car. It then went to the quenching tower. Here a 12000 gallon deluge of water cooled the charge so it could be graded and stored for dispatch.
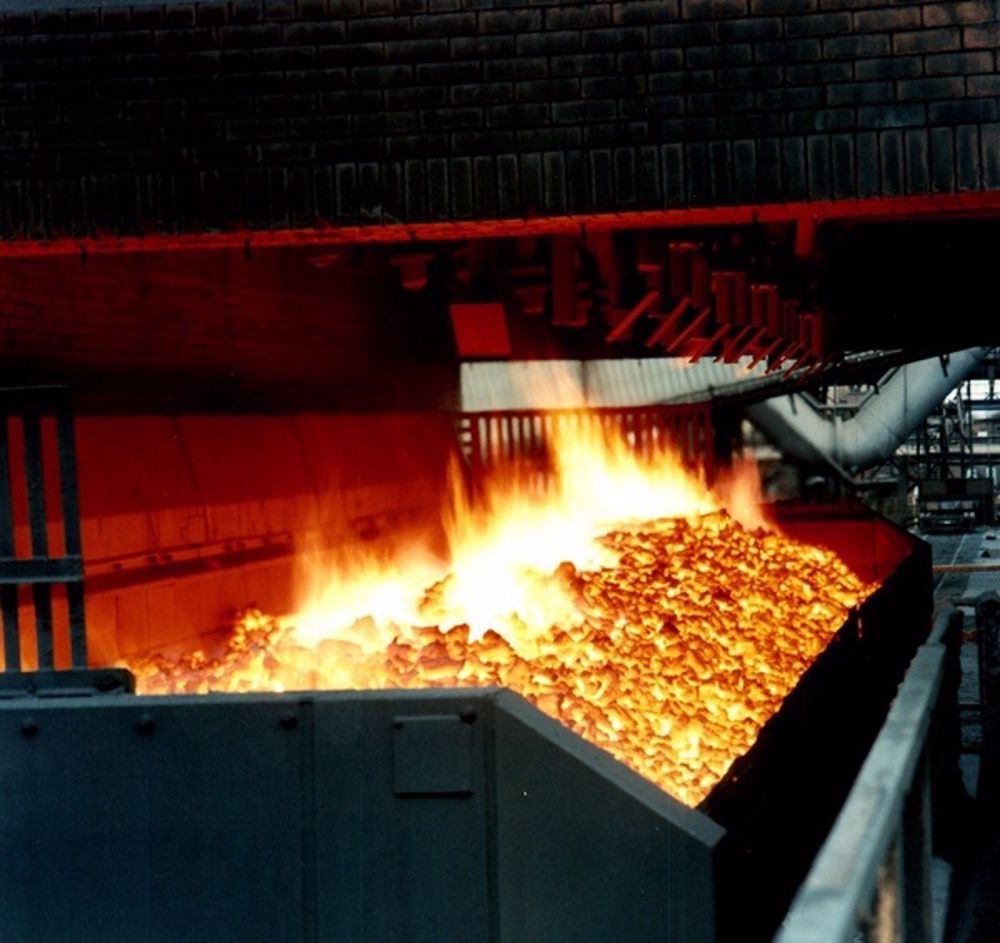
The overall process is outlined in the following diagram:
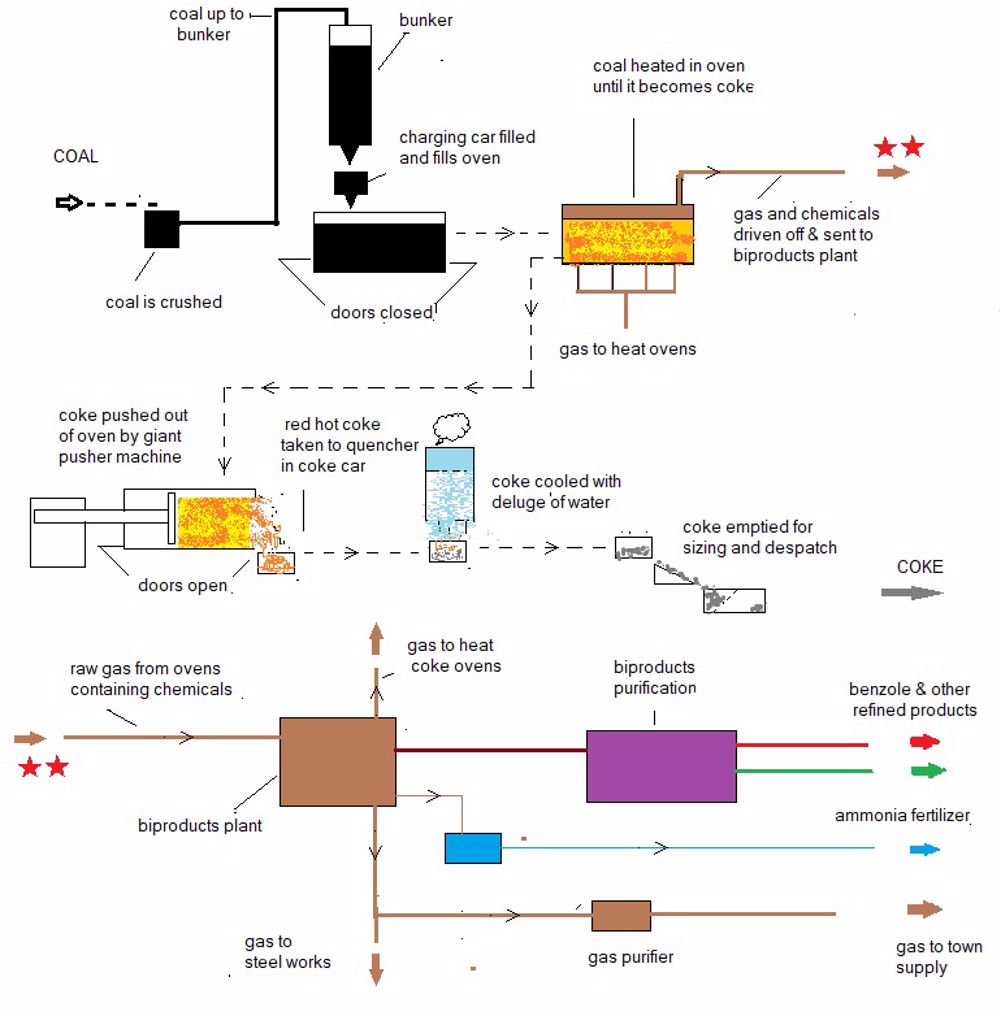
Biproduct recovery
The volatiles from the ovens were collected in mains that run above the ovens on each side. As many solid particles were entrained in the volatiles these mains were flushed with recycled liquor and routinely kept clear of build-up manually by using rods with small spade ends accessed through plugs on the top of the mains. (I recall doing this job during my apprenticeship and by the end of the shift my chest would be soaked in tar). The stream of volatiles was drawn through the whole biproducts section by a turbo 'exhauster' .
Though some differences exist between plants, the purification train consisted generally of the following:
1 Separation of the flushing liquor
2 Primary cooling
3 Exhausters
4 Tar removal (e.g. electrostatic detarrers)
5 Naphthalene washers
6 Secondary coolers
7 Ammonia washers
8 Benzole scrubbers
9 Secondary naphthalen washers
10 Gas purification
11 Gas holder
12 Booster to grid via meter and drier
These stages are shown on the following diagram:
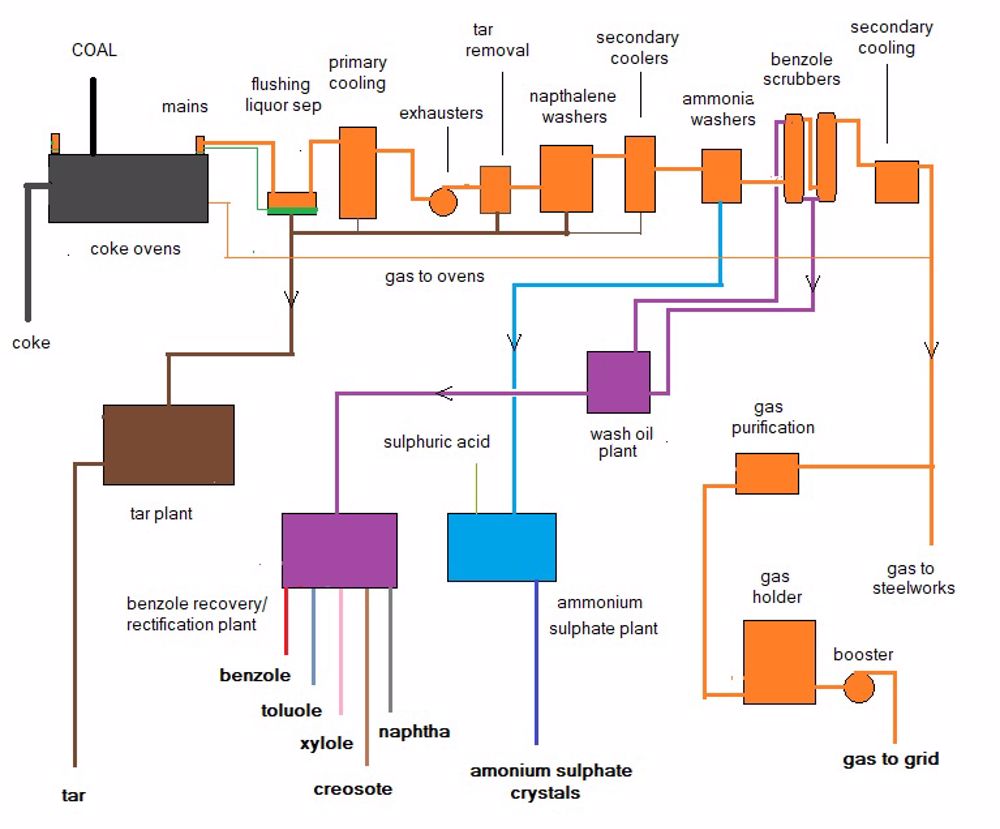
Therefore in addition to coke and gas, carbonisiation of coal yields many valuable products. Coal chemicals have an extremely high carbon content, and their molecular structure makes them ideal materials to be transformed into pure carbon and graphite. This is particularly useful in applications where metals cannot meet the high-temperature or chemical-resistance requirements.. Many compounds containing pure carbon can be found in high-tech applications: high temperature smelting, carbon reinforced disc brakes, electrodes in Li-ion batteries and brushes for electric motors. Carbon black improves and extends the life of tyres thereby reducing waste. Highly porous activated carbon is also used in environment and health protection applications and medical devices such as high end face masks- naphthalene is converted to phthalic anhydride and polyester resins for use in paints and reinforced polyester applications. Creosote is biocidal wood preservative.
Future
Coal has been the backbone of our economies since the start of the industrial revolution and as described above has produced chemicals which have been key ingredients in many industrial activities and made possible by the application of chemical engineering even at a time when this discipline was not known as such.
Now with ever increasing awareness of the need to achieve a 'green' environment the chemicals derived from coal and even the processes of producing them are becoming unacceptable and essential products such as road pitch and benzole are derived from other sources.
Coke has been a key component of iron production. However now the aim is to achieve low/zero carbon economies so future development is based on new processes which eliminate the need for coke. An example is the FINEX process being developed at the giant Korean Posco plant which produces iron direct from a mixture of ore and coal in a fluidized bed. Coke ovens require coking coal (i.e. coal of a grade which will carbonise satisfactorily) but the new processes could take coal of wider specification which in itself will reduce carbon footprint.
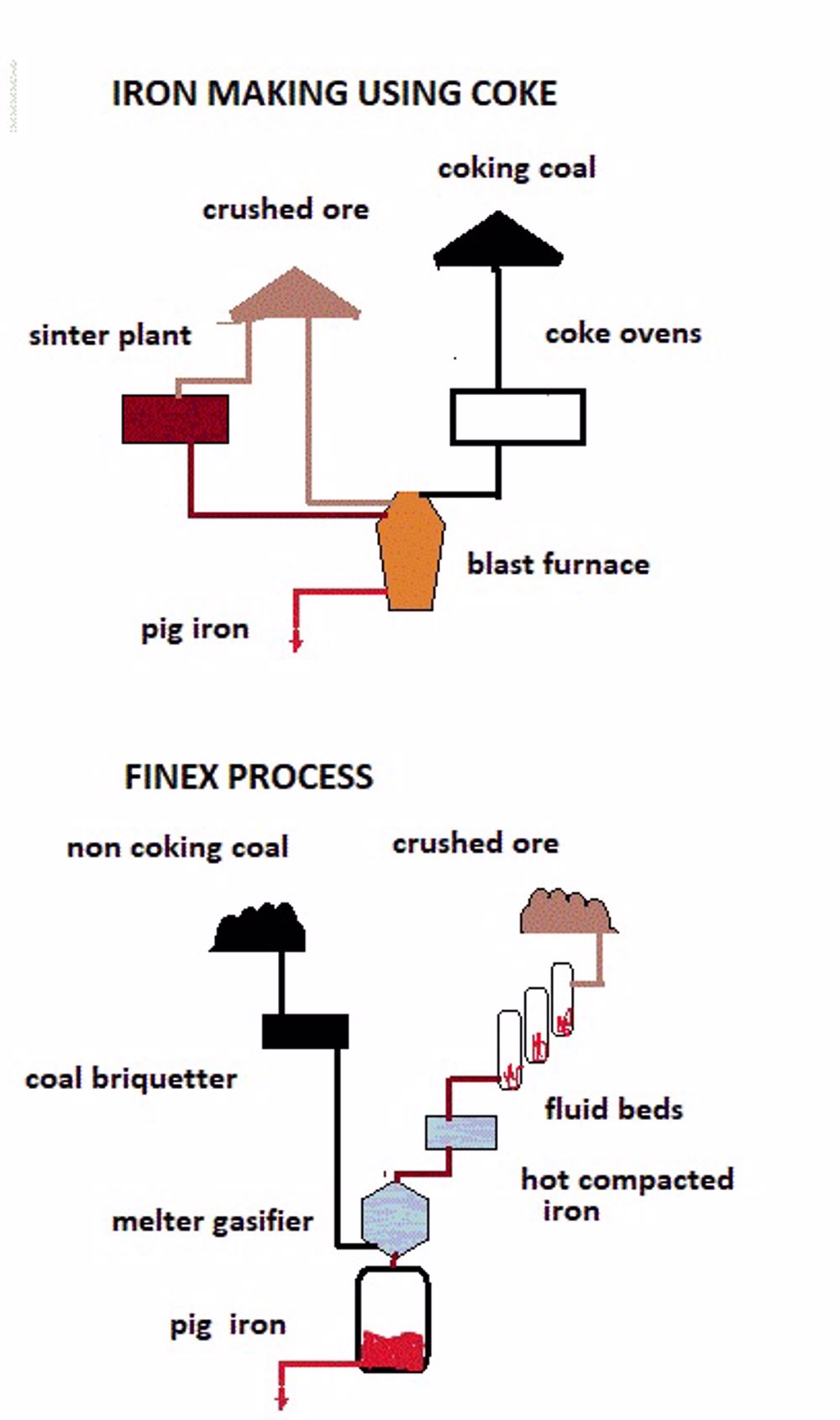
Now the future will be one of constant improvement with ever increasing demand for the skills and ingenuity of the chemical engineer.