The Wonder of Coal and its Products
1000 feet underground in a hot, close, dusty atmosphere I was crawling with a colliery deputy (assistant manager) a long way through a space three feet high towards the coal seam 18 inches deep from which coal was being dug. It may seem strange why a seam so thin was being worked but this was Durham coal from which the finest coke could be produced.
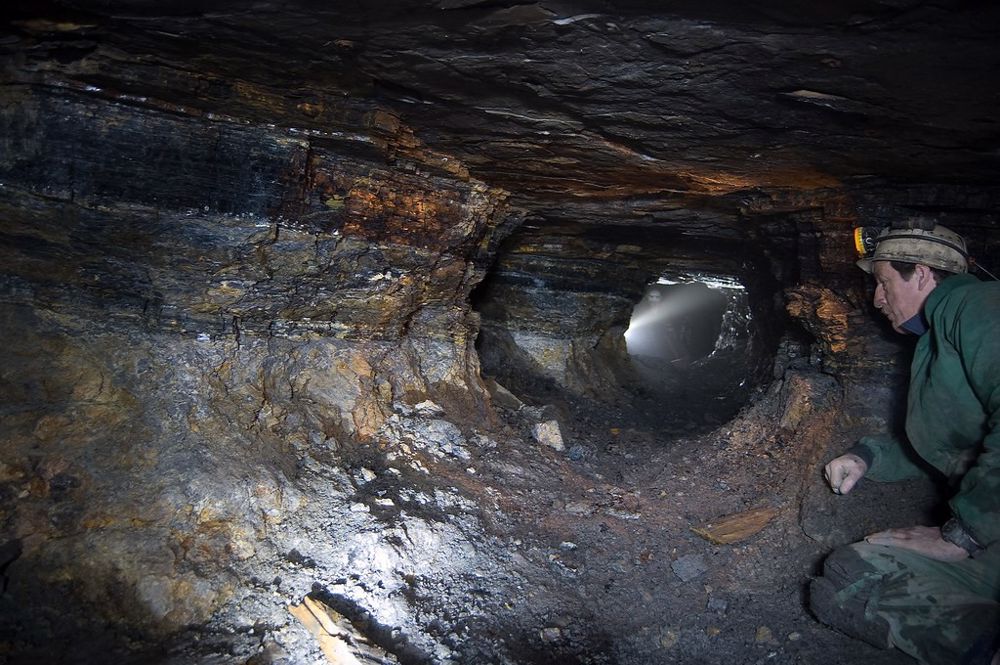
As a chemical engineering student I was on my vacation experience at the newly built Fishburn coke oven plant which was high above our heads and I was a lodger in the kindly, quiet, powerful deputy's home.
As detailed in the journal of Daniel Defoe and in the diary of Samuel Pepys, in the 17th century coal from Newcastle was important even then and later became the raw material on which the modern industrial age was built .
From Victorian times to the discovery of North Sea oil and gas, Britain relied on coal and not only for power and transport. Manufacture of town gas provided the first effective street lighting (and still existed in many places when I was young). This was the first energy and lighting to be delivered direct into homes, and as a secondary product gave coke, a smokeless fuel (some of which was used to power locomotives and reduce smoke in the early days when there were still open passenger carriages).
The iron and steel industry used vast amounts of coal of the right grade to provide high grade coke for blast furnaces in which iron was made and for foundries where iron was cast. This iron together with scrap was used in the manufacture of steel.
However coal was also a way of life.
The rigours and hardship of a daily life underground built a society like no other; brass bands, art, competitive gardening (leeks) and pigeons were among the favourite obsessions of the mining community. While the positive side of community and neighbourly help was the key feature, the downside was the environment it created. The pit heaps containing the spoil from the mining process were a great attraction to children but also deadly dangerous. Massive cavities below the surface by the combustion of waste coal were a death trap to children to whom pit heaps with their fine crops of luscious blackberries were irresistible.
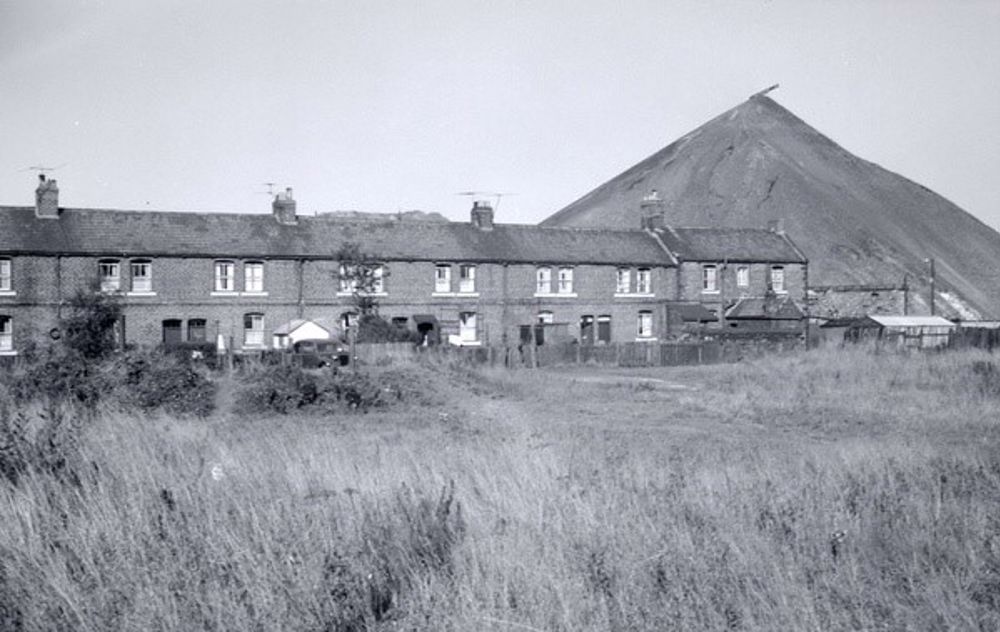
The worst incident was on 21st of October 1966 in Aberfan, Wales, where a whole pit heap, which had been foolishly laid on streams, cascaded down upon a school killing 116 children. So the source of the material which gave so much had its downside.
A diversion from this was the open cast system. This is huge in Australia but also practiced in the UK where coal nearer the surface could be dug out after massive earth removal and the area then restored: objected to by environmentalists but safer and in some ways more eco-friendly than deep mining.
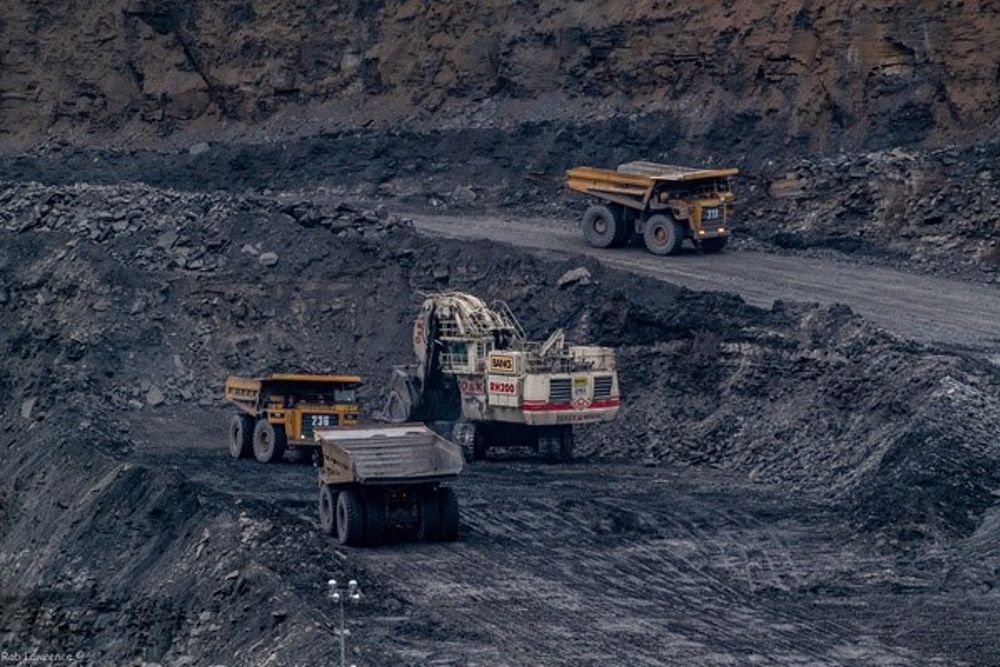
When I was young the air particularly in winter hung heavy with the smell of coal which when the atmospheric conditions were right created intense smog some so thick that a cycle lamp could not light the road below.
So on that day at Fishburn, deep underground, I was seeing the coal mined to feed the Fishburn coking plant. But coke had been produced in County Durham for many years.
Three weeks before my descent into the Fishburn pit, I had visited the long abandoned beehive ovens at Rowlands Gill south of Newcastle, small brick chambers shaped inside like the old fashioned bee hives . After Abraham Derby in 1709 had first smelted iron using coal instead of charcoal, beehive ovens spread across Britain and the industrialised world. These beehive ovens gave an excellent massive pieces of very hard coke but were labour intensive, limited in output, wasteful and highly polluting.
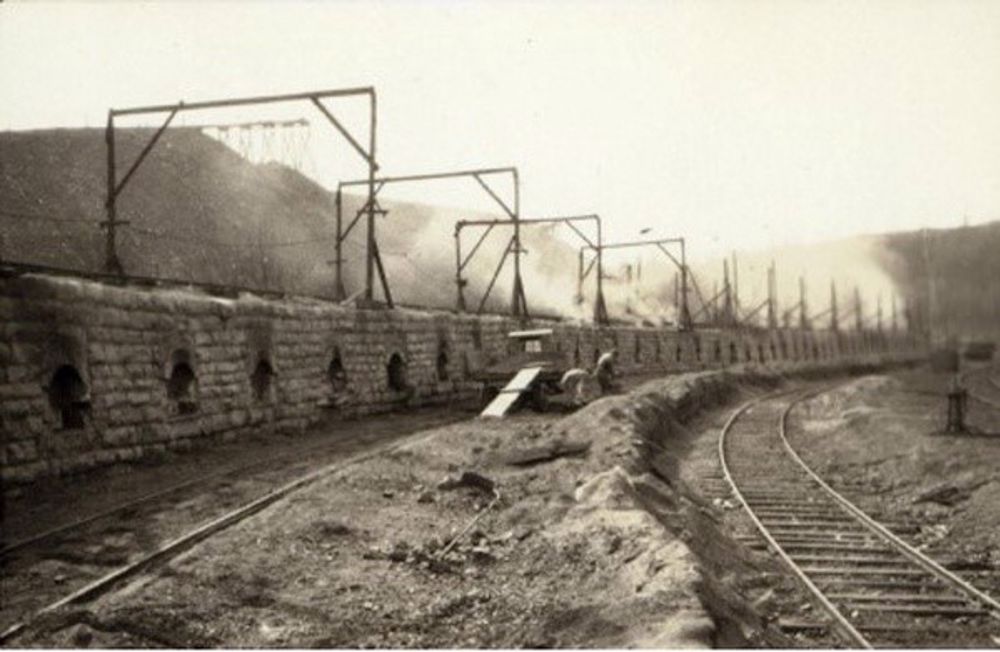
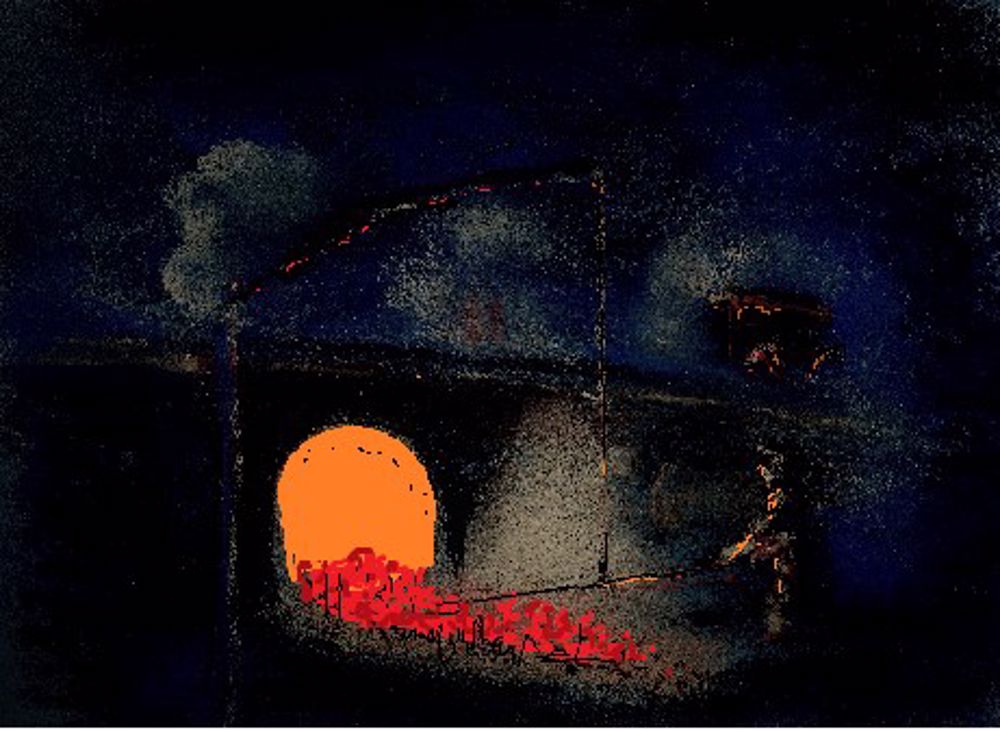
Finally after much chemical engineering development, coke oven plants were built which not only gave high quality coke but also recovered the gas and the many valuable chemicals present in coal. The process is shown in the following diagram.
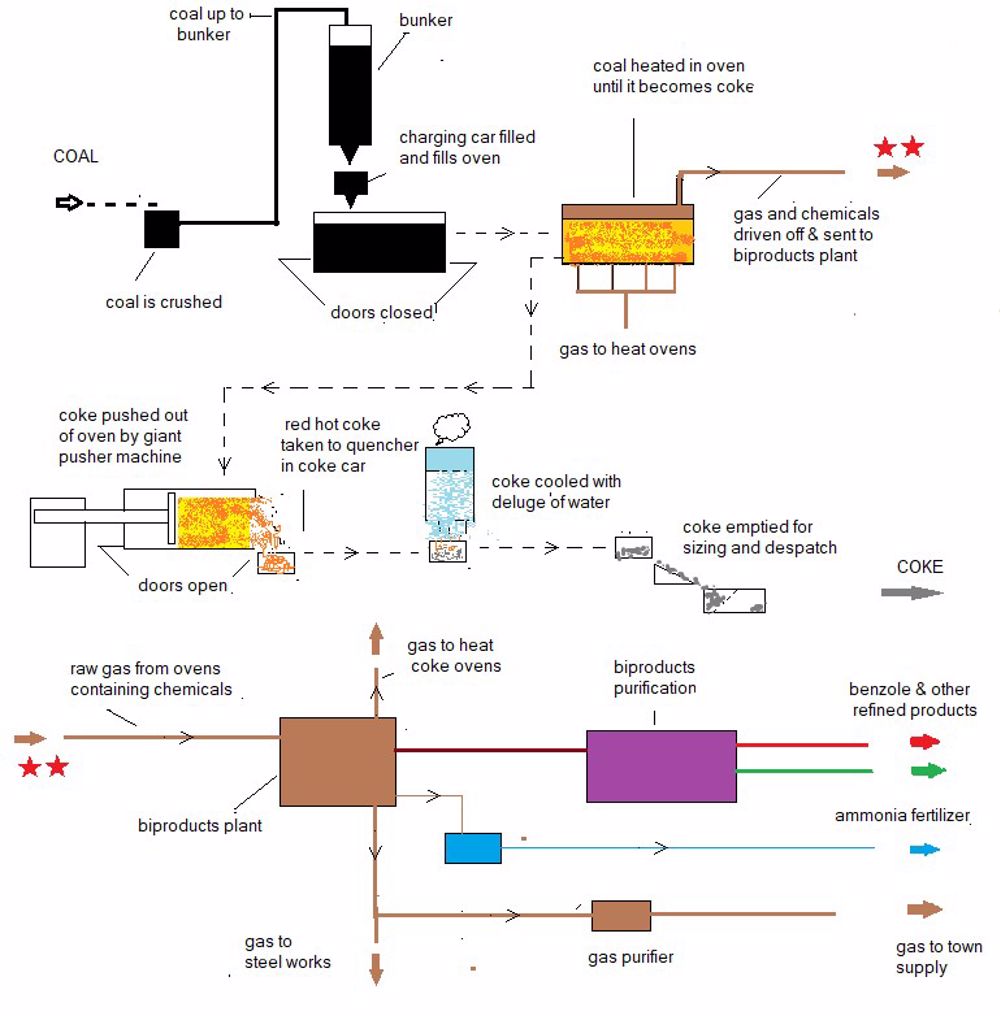
The raw material was coal and the plant produce excellent coke suitable for steelmaking, gas which was used to heat the coke ovens and for other works' use and the surplus sent to the town's supply.
The coking plants which were built on steelworks sites were integrated with the steel works to achieve the greatest efficiency in the production of iron and steel.
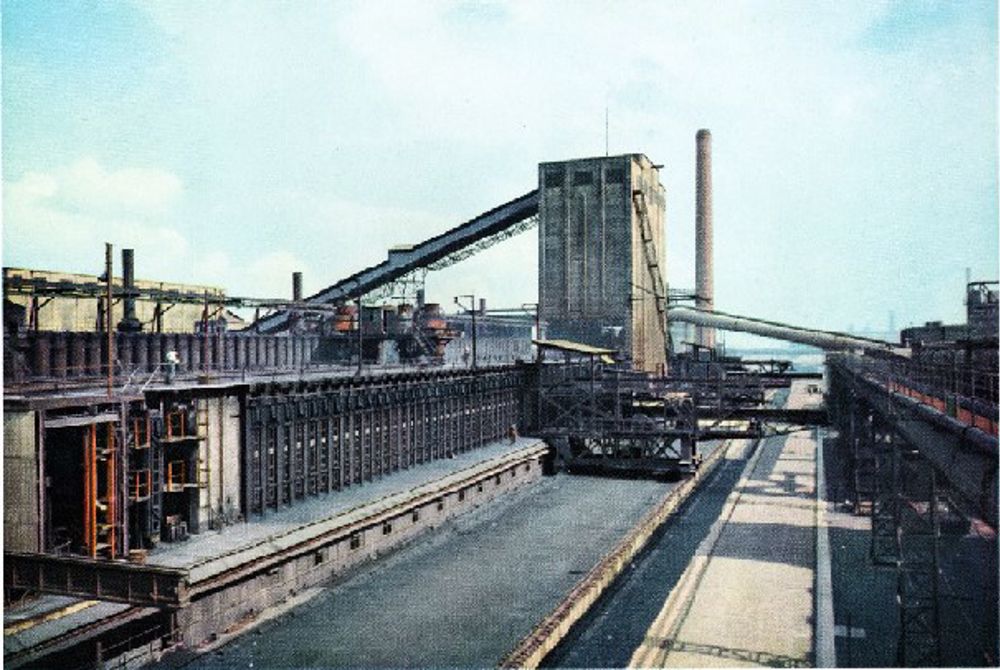
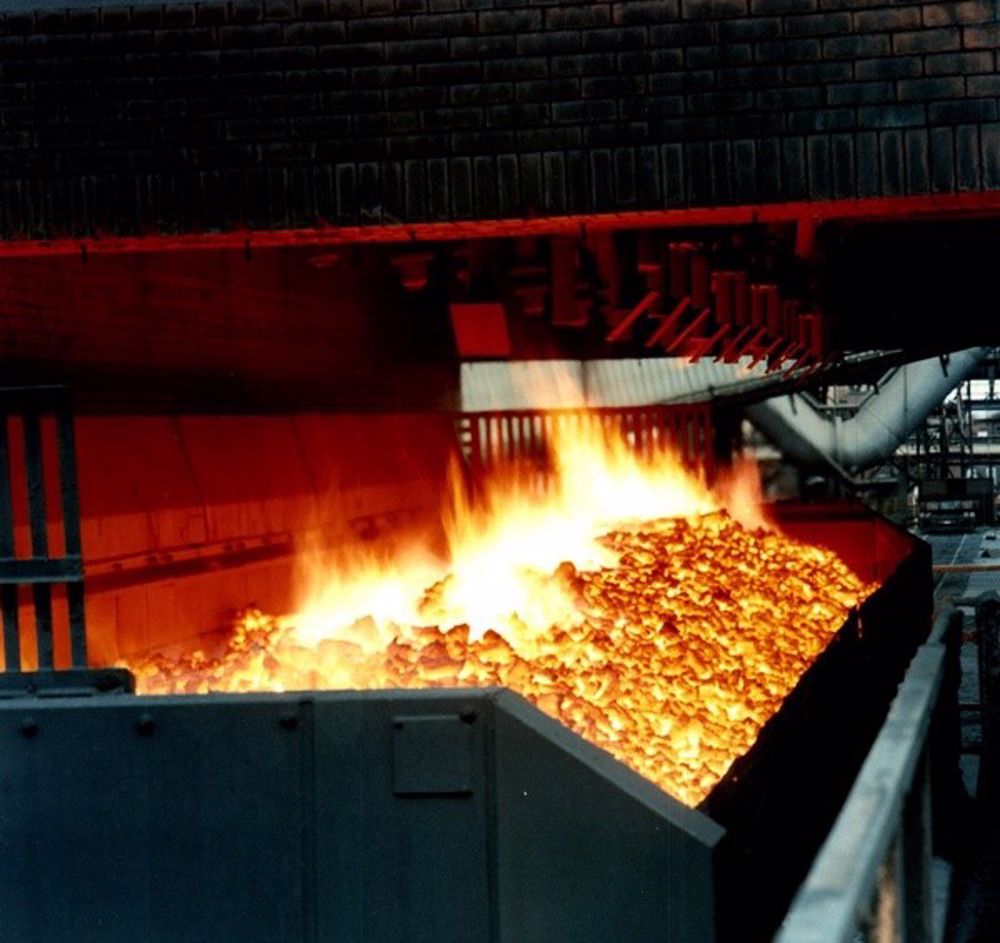
By the application of sound chemical engineering, the chemicals from the coking process have been refined to give products which have formed a key part of our industrial economies.
The chemicals have included tar for roads, benzole, creosote, ammonia fertilizer and many others.
However in our environmentally conscious age many of the products from the coal carbonisation process are now considered unsuitable and have been replaced by similar products from the refining of oil.
The coking plants had their effluvia from the quenching towers, the atmospheric pollution as the ovens were emptied and the run offs polluted rivers and streams.
It was inevitable that while coal and its products had been the backbone of our prosperity, in the present age the situation had to change. As an example the Derwenthaugh coke works near Newcastle upon Tyne which I knew as a student is now a beautiful country park bisected by the lovely clear waters of the River Derwent. As with the steam locomotive loved by so many of us, the dramatic spectacle of the coke works will disappear and other means are being found to satisfy the demand for energy and materials
Steel will long be required for most of our needs from bridges and ships to cars and domestic appliances and iron is required to make steel. But in striving to reach a zero carbon environment new processes are being developed which will remove coking altogether so the coking process which has been key to our development and lifestyle will become a thing of the past.
Engineers have used their knowledge, skill and initiative to benefit society from what coal has to give and they will continue to do so in the new technology of the future.