Chemical Engineering and road transport
It is a cold, dark night as the large articulated road tanker rolls through the gates of the customer's works and backs up to the discharge point. The driver, highly trained and experienced, raises the rear compartment shutter exposing the array of pipes and valves, connects the large diameter reinforced metal hose to the filling point and carries out the purging routine. He starts the pump and the transfer of the liquid oxygen from the tanker to storage begins, the hose and pipework soon cooled by the cold liquid to provide a thick layer of insulating frost.
Half an hour later , checks done, one satisfied customer's delivery completed and the driver is on his way through the freezing night to the next customer .
Transport management is about customer service whether this is to outside customers or internal within a company.
It includes the following -
Scheduling - ensuring deliveries are made on time via the safest and most economical route and providing the driver with the correct paperwork.
Driver selection and training - drivers are working away from base; they are responsible for their vehicle interfacing with customer, with base and with the public. They are independent and self reliant
Vehicle safety and maintenance - satisfying the authorities on the vehicles' road worthiness whether in MOT or in roadside checks. Both automotive maintenance and maintenance of on board 'plant' in the case of tankers
Vehicle design and construction - compliance with Vehicles Construction and use Regulations and compliance with appropriate regulations for international travel.
Where bulk liquids are carried, particularly pressurised systems or cryogenic liquids, CHEMICAL ENGINEERING enters.
A cryogenic tanker is almost a process plant on wheels. In addition to the necessary vehicle dynamics , this cryogenic equipment has to handle, store and transfer liquified gases at temperatures below minus 180 degrees centigrade. From the early days when tanks were relatively small 'teapot like' mineral wool insulated copper vessels mounted on small lorries, the tanker has been developed into large units with aluminium alloy vessels and equipment of the highest order. The chemical engineering behind this has had to ensure the equipment maintains its strength at temperatures where the physical properties of many metals change, keeps the integrity of the vessels and pipework at high pressures and ensures by double tanks with a high vacuum between them that pressures do not rise to a level which would cause product loss, over pressurisation and danger to the public and employees.
At the filling facility the tanker product quality is checked and the tanker weighed to ensure no overloading.
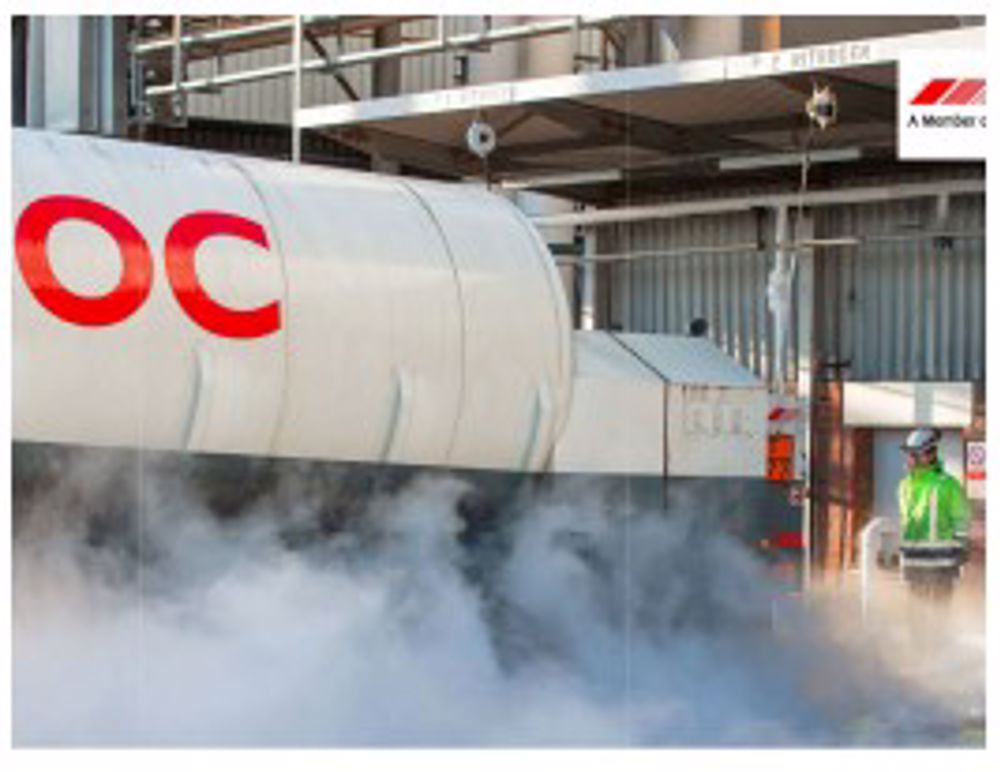
Engineering to high standards is required at the filling facility to ensure the safety and control of the filling process and at the customer end whether it be hospital, process plant, food production or engineering works. The customer installation is engineered to ensure proper product storage without loss and giving an instant online service.
With road tankers an additional problem is the massive swilling movement of the load particularly at roundabouts. Careful design of internal baffles is essential to prevent violent movement of the heavy load which could result in the tanker overturning. (even more critical with a tanker carrying liquid oxygen where spillage can result in atmospheric enrichment and a disastrous fire of combustibles).
Similarly transport of other cryogenic liquids such as nitrogen, helium, compressed gases, fuels and many chemicals where equipment interfaces with the public rightly demands a high level of practical chemical engineering skill in addition to the expertise of the automotive engineer.
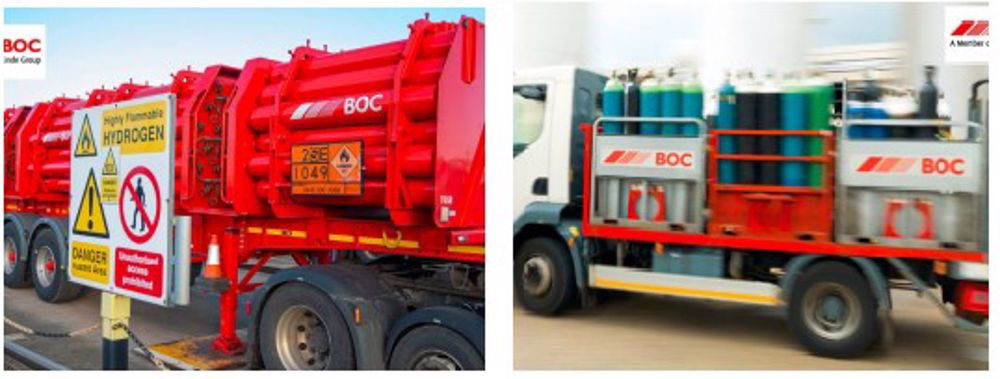
While every precaution is taken on design, construction and use, accidents can occur. This is not a case of a static load just thrown on to the carriageway. The tanker on its side with possible leakage and damage can cause sudden pressurisation which could be lethal. A team must be available to work closely with the emergency services and with an intimate knowledge of this 'mobile plant ' can ensure an accident does not become a catastrophe. As with any process plant, training, and emergency drills are key.
What of the future? With the push to zero carbon, the automotive technology must and will change. The requirements to achieve safe, efficient and economical bulk liquid product carriage will continue to be the application of sound chemical engineering and provide ample opportunity for the young engineers entering the field.