Beware of the toe cutter – How to maintain a Jury’s attention
A key unit operation at the Hydrocarbon Products Pty Ltd (HPPL) styrene monomer plant at West Footscray was a 180ft, 12.5ft diameter distillation column, fitted with 100 sieve trays to separate a mixture of 60% styrene monomer (SM) and 40% ethyl benzene (EB) by the difference in their boiling points. EB/SM feed entered about a third of the way down the column joining liquid falling from the tray above.
Each tray had an 18-inches liquid holdup and as liquid fell down the column it became richer in SM, while rising vapour was richer in EB. At the bottom of the column a steam heated reboiler provided the necessary vapour to achieve EB/SM separation and also SM product was drawn from column bottoms to remove polymers. Column overhead vapour was condensed by cooling water with partial rundown to EB storage, and the bulk of the stream returned as reflux to the column's top tray.
The plant capacity of 100,000tonne/year styrene monomer, the relative closeness in boiling points (EB boils at 136°C and SM at 145°C) and the operating pressure of –85kPag required to limit column bottoms temperature below 100°C to minimise SM polymerisation, determined the vessel’s dimensions. The EB/SM Splitter with its 36-inch vapour outlet pipe was clearly visible from the top of the West Gate bridge as I drove to work each morning.
In mid 1981 I was appointed technical lead for a project to replace the 100 sieve trays with 6 x 24ft beds of Sulzer Mellapak structured packing in the EB/SM Splitter. Justification of this project was reduced column pressure drop, which increased product yield of SM by 1% by reducing bottoms temperature by 10°C and a reduction in reboiler steam usage. Part of my role was to convince Monsanto’s distillation technical specialist (a world authority on distillation with references in Perry, the chemical engineers' bible) that the liquid distributors proposed by Sulzer (supplier of tower internals) would provide a uniform liquid distribution across the large diameter EB/SM Splitter.
When I visited the St Louis office he was concerned that because of the large diameter of the splitter, the static liquid head in the distributors would only be about 23mm for the specified 6mm diameter liquid distribution drip points, compared with about 227mm for a liquid distributor with 3mm diameter drip points as proposed for the Monsanto Company 30ft diameter EB/SM Splitter at Texas City, also to be packed with Mellapak (supplied by Koch Engineering and licensed from Sulzer).
In the end St Louis did sign off on 6mm drip points with some reservation, but the Sulzer distributor design turned out to be symmetrical so that level tolerance only applied to half the splitter diameter, doubling allowable out of level tolerance. I personally checked all of the 6 distributors with a dumpy level to confirm out of level tolerances were met as part of the column’s commissioning (see attached photo).
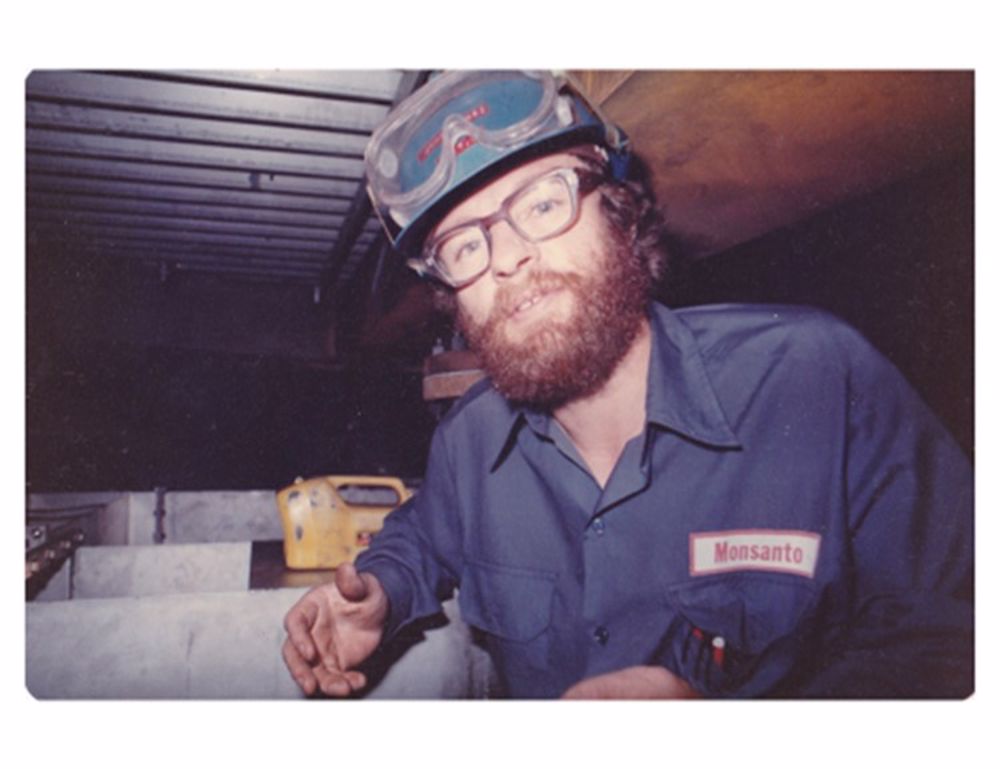
Seven years later I found myself in the witness box of a St Louis court supporting Monsanto in a lawsuit against Koch for their supply and design of the Texas City 30ft diameter EB/SM Splitter packed beds, which had never operated to design due to plugging of the 3mm liquid distributors with iron oxide (rust). Monsanto won the case on the basis of evidence from a metallurgist (a professional witness) who was able to convince the jury that plugging was caused by a form of iron oxide, that could have only been formed during fabrication of the packing’s 0.3mm thick carbon steel sheets (i.e. at high temperatures (greater than 300°C) compared with maximum operating temperatures (about 100 °C), which Koch should have removed from the sheets prior to packing fabrication. Luckily, I wasn’t questioned on my St Louis distillation expert's meeting.
My Australian accent was enjoyed by all and possibly led to me being asked during cross examination by Koch’s attorney, who didn't appear to know what line of questioning to subject me to, “what is a toe-cutter”?
While the internet was yet to be discovered in 1982, we did have a computer link between the West Footscray plant and Texas City, which we used to exchange technical information and a little bit of conversational chat between my Texas City technology contact and me. At the time when Texas City were struggling to restart their EB/SM Splitter, Monsanto head office sent an emissary with a mission to cut staff numbers severely worldwide including at the West Footscray plant.
A popular Australian movie Mad Max released in 1979, included as the main antagonist the leader of a merciless motor cycle gang who terrorised the Australian outback. This seemed a fitting title for our ruthless visitor and I passed on a warning to my Texas City contact “to beware of the toe-cutter” as he was visiting Texas City next.
A hard copy of this conversation was provided to the Koch legal team and so became a leading question during my time in the witness box.
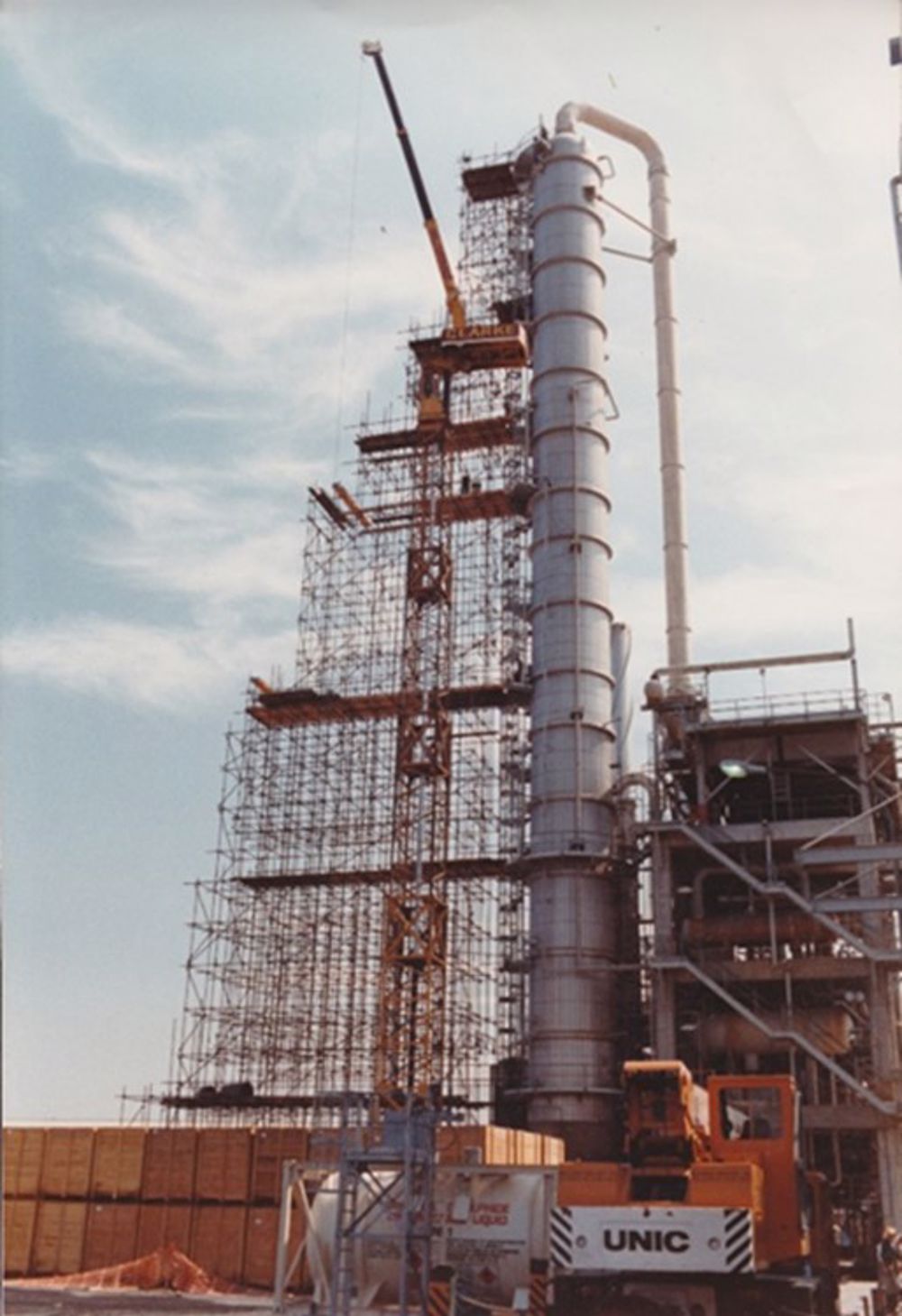
Resources:
1. Monsanto Company Report
2. Personal experiences 1981-1988
3. Personal Photos